Custom Black | Hard Anodized Aluminum Profiles Extrusion
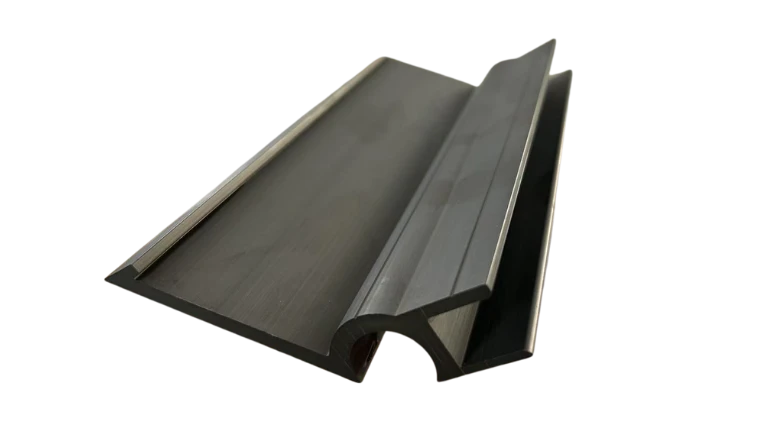
Hard anodizing, also referred to as hard coat anodizing, is an advanced electrochemical process that significantly strengthens aluminum surfaces. Unlike standard anodization, hard anodizing creates a thicker and denser oxide layer that provides exceptional wear resistance, corrosion protection, and improved performance under extreme conditions.
This process is especially vital for industries relying on aluminum profiles in demanding environments, as it ensures the profiles remain durable and maintain their structural integrity even under heavy use.
Another key difference is the color. While standard anodizing often results in a lighter finish, hard anodized aluminum naturally has a dark gray to black appearance due to the dense oxide layer. This makes it ideal for creating black aluminum profiles that not only offer exceptional strength but also a sleek, professional look.
Thickness of Hard Anodizing Oxide Layers
The oxide layer thickness achieved through hard anodizing far surpasses that of standard anodizing. Hard anodizing can produce oxide layers ranging from 25 to 150 microns, depending on the specific application and process parameters. This thick and dense layer provides exceptional hardness and resistance to wear and corrosion. In contrast, standard anodizing typically produces a thinner oxide layer, usually between 5 to 25 microns, which is sufficient for decorative or light-duty applications but lacks the durability required for demanding environments. This significant difference in oxide layer thickness makes hard anodizing the preferred choice for industrial and high-performance uses.
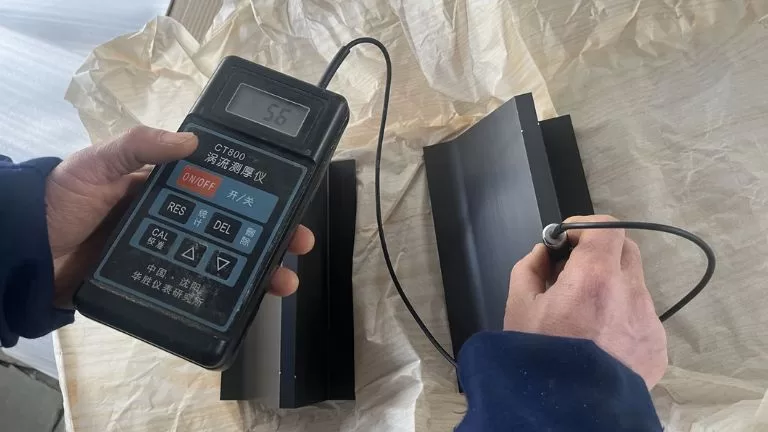
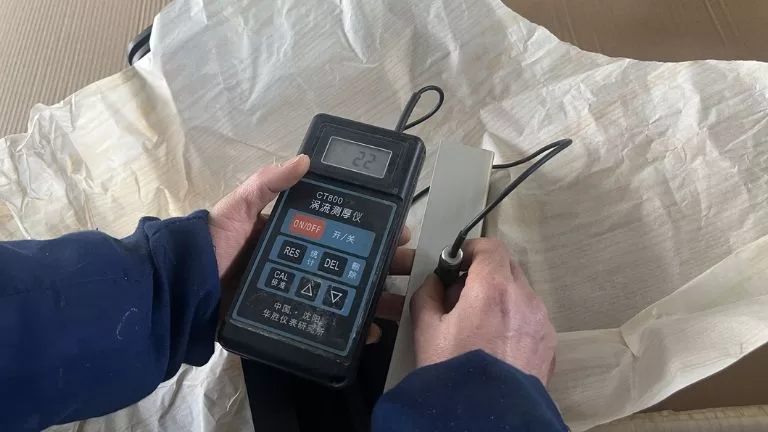
The above aluminum profiles are used for the same project, with hard anodizing applied for outdoor use and regular anodizing for indoor use.
Hardness of Hard Anodized Oxide Layers
The oxide layer produced by hard anodizing is renowned for its exceptional hardness, making it ideal for high-performance and industrial applications. The hardness of the oxide layer can reach up to 400-600 HV (Vickers Hardness), depending on the alloy and process parameters. Compared to standard anodizing, which typically achieves a hardness of 200-300 HV, hard anodizing provides significantly greater wear resistance, scratch resistance, and durability. As a result, hard anodized aluminum is commonly used in applications requiring high durability, such as aerospace, automotive, and machinery components. The hard and thick oxide layer ensures long-term performance even in harsh or heavy-use environments.
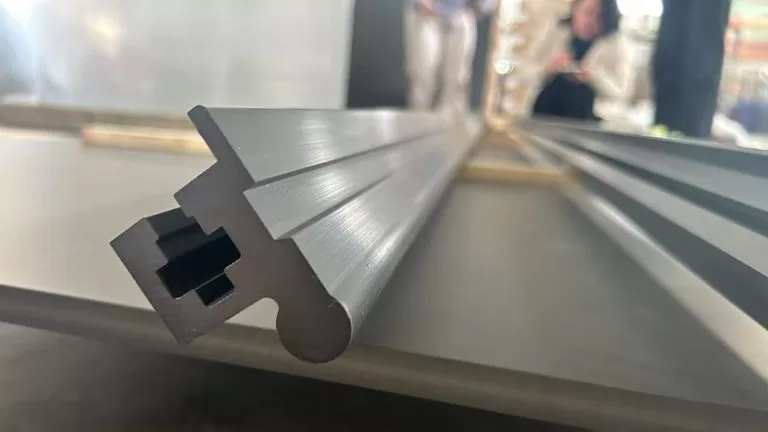
Thermal and Electrical Properties
The hard anodized oxide coating offers remarkable thermal resistance, making it suitable for applications involving high temperatures, such as heat exchangers, industrial machinery, and electronics housings. This durable oxide layer ensures stable performance even under elevated thermal conditions, enhancing the longevity and reliability of the components. Additionally, the hard anodized surface provides excellent electrical insulating properties, which are highly beneficial in applications requiring non-conductive materials, such as electrical insulators and housings for electronic components. These combined thermal and electrical properties make hard anodized aluminum a versatile material for demanding industrial and technical applications.
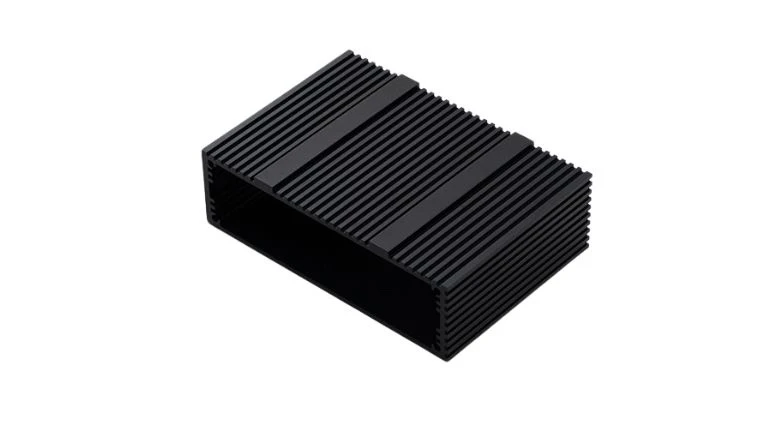
Better Corrosion Resistance
The thick and dense oxide layer created by hard anodizing provides excellent corrosion resistance, effectively protecting aluminum from chemical exposure, saltwater, and moisture. With a coating thickness of 25 to 150 microns, hard anodized aluminum is ideal for marine environments, industrial applications, and outdoor use, where it withstands harsh conditions. In salt spray tests, it can resist corrosion for up to 1,000 hours or more, ensuring long-term durability even in extreme environments.
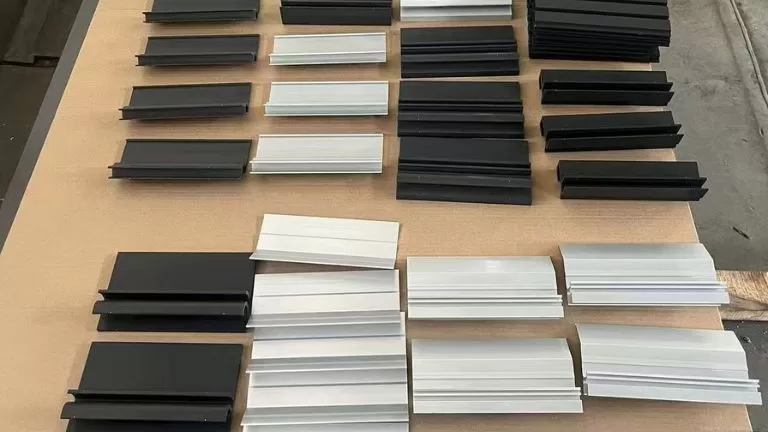
Custom Hard Anodized Aluminum Profiles
We specialize in providing custom hard anodized aluminum profiles designed to meet your specific requirements. With 40 advanced extrusion production lines, including a 6000-ton extrusion press—one of the largest available—we have the capability to produce aluminum profiles in a wide range of sizes and shapes. To ensure a complete and efficient supply chain, our facilities are equipped with comprehensive post-processing services, including machining, cutting, drilling, tapping, and surface treatments, tailored to your specifications. This combination of large-scale production capacity and precise secondary processing allows us to deliver high-quality aluminum profiles suited for diverse industries, such as aerospace, automotive, construction, and electronics.
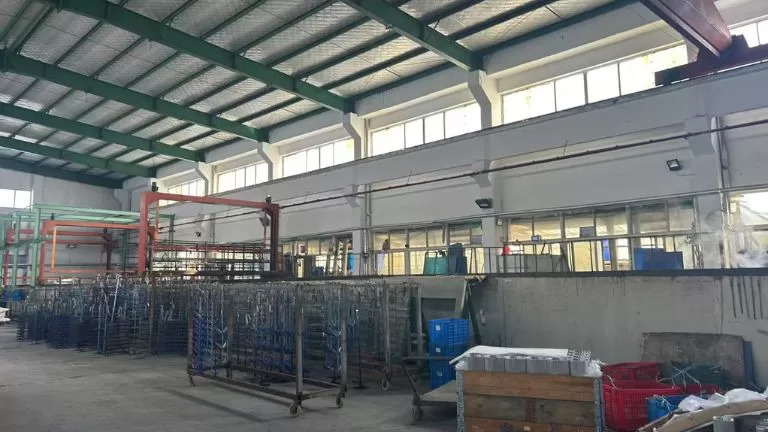
Our Factory
HTS NEW MATERIALS stands as a premier aluminum extrusion profile manufacturer in China. Boasting more than 40 production lines and housing the largest 6000-ton extrusion press, we excel in delivering high-quality solutions. Our capabilities extend to mold design and processing, along with comprehensive surface treatment and advanced machining services.
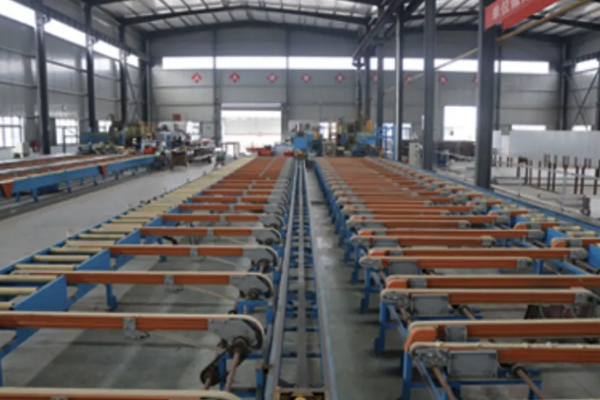
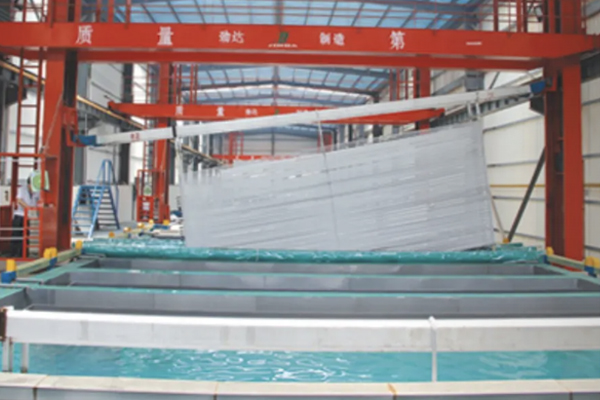
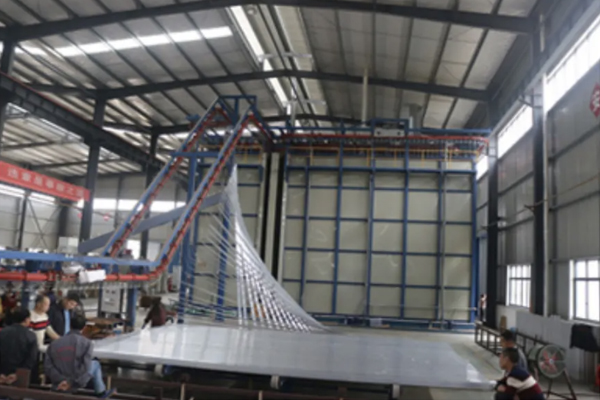
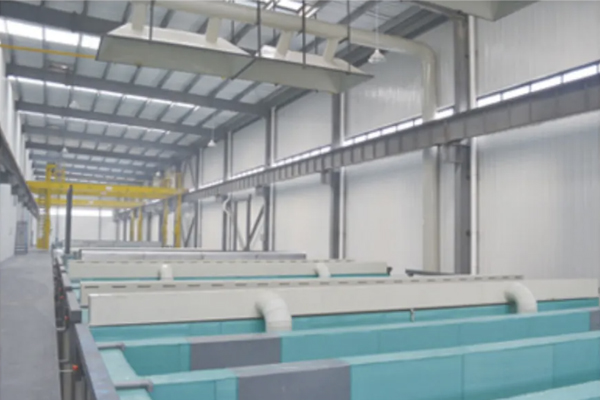
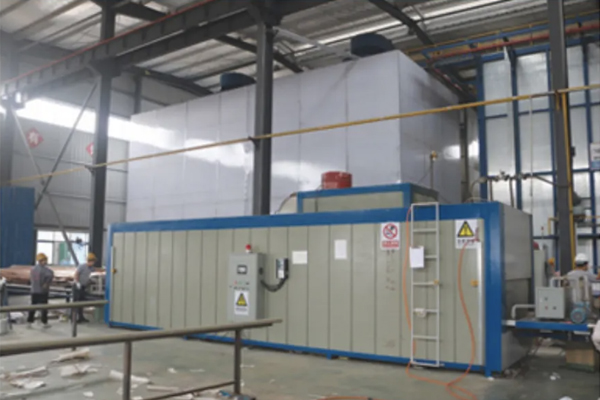
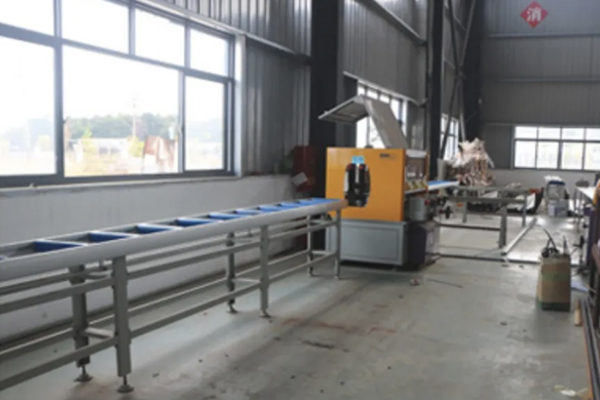
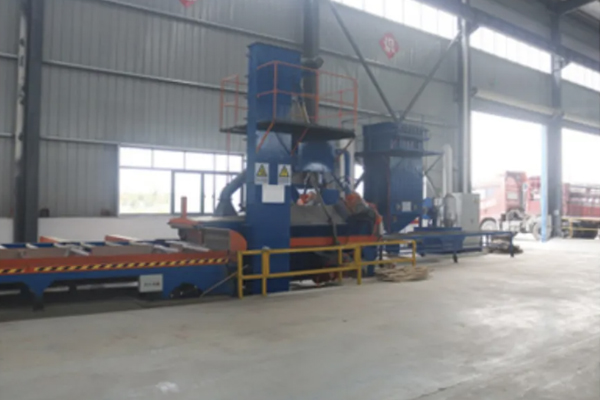
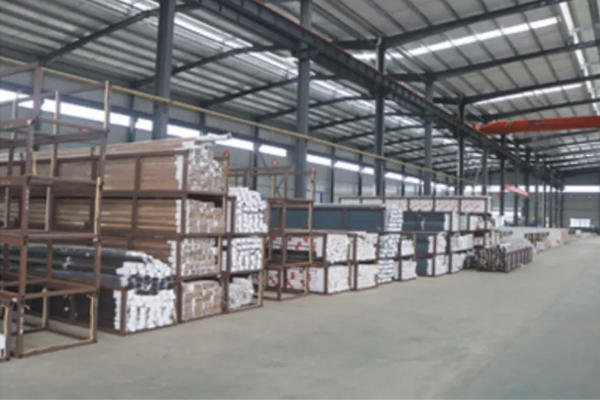
Get a Quote Now
Custom Aluminum Profile Process
Step 1: Our engineer will review your detailed size or drawing and provide a cross-sectional drawing for your confirmation.
Step 2: We open dies for your custom extrusion, create a sample, and send it to you for approval.
Step 3: If modifications are needed, we adjust the die size until you are satisfied with the sample.
Step 4: We inspect the raw material using a spectrum analyzer and proceed with extrusion production, providing weekly progress updates.
Step 5: Depending on your desired surface finish, we offer anodizing, electrophoresis, powder coating, or PVDF options.
Step 6: To ensure safe transportation, we carefully pack your products to avoid any damage.
RFQ
The combination of durability, resistance, and customization makes hard anodized aluminum profiles suitable for a wide range of industries:
1. Aerospace and Automotive
- Structural stability is critical in aerospace and automotive applications. Hard anodized aluminum profiles are used in load-bearing elements and critical system components due to their strength and lightweight nature.
- Common applications include aircraft seat tracks, car chassis components, heat exchangers, and hydraulic systems.
2. Heavy Machinery and Industrial Equipment
- In factory setups, aluminum profiles are often used as support structures, conveyor systems, and assembly line components.
- Hard anodizing protects these profiles from wear and tear due to repetitive motions, friction, and harsh working environments.
3. Electronics and Semiconductor Industry
- Hard anodized profiles are commonly used in heat sinks, electronic enclosures, and circuit board mounts, thanks to their insulating properties and thermal resistance.
4. Marine and Outdoor Equipment
- The high corrosion resistance of hard anodized aluminum makes it well-suited for marine applications, such as boat equipment, railings, and outdoor furniture, where it endures prolonged exposure to moisture and saltwater.
5. Architecture and Construction
- In architectural design, aluminum profiles are used in curtain walls, frames, and decorative elements. Hard anodized profiles ensure longevity while offering modern and attractive finishes for buildings and structures.
6. Medical and Laboratory Equipment
- These profiles are also popular in medical devices and laboratory equipment due to their non-toxic, sterile, and corrosion-resistant properties.
The primary aluminum alloys used for extrusion belong to the 6xxx series, specifically 6061, 6063, 6060,6082 and 6066. These alloys are highly favored due to their excellent extrudability, good mechanical properties, and corrosion resistance.
- 6061: A versatile alloy with higher strength, suitable for structural and transportation applications.
- 6063: Known as the “architectural alloy,” it offers excellent surface finish and is widely used for decorative and structural purposes.
- 6060: Similar to 6063 but with slightly lower strength, ideal for intricate and thin-walled profiles.
- 6066: A high-strength alloy within the 6xxx series, often used in more demanding structural applications.
- 6082: A strong alloy with better mechanical properties compared to 6061 and excellent corrosion resistance, commonly used in high-load structural applications and in marine environments.
The 7xxx series alloys, such as 7075, are used in applications requiring extremely high strength and performance, such as aerospace and high-end engineering projects. However, they have lower corrosion resistance when compared to 6xxx alloys and are therefore less commonly used for general extrusion applications.
While 1xxx, 3xxx, and 5xxx series alloys can be extruded, they are generally used infrequently for extrusion due to their lower strength or other limitations compared to 6xxx and 7xxx alloys. These series are mainly used in specialized applications. Additionally, if extrusion products from these series are requested, higher minimum order quantities (MOQ) are typically required for custom production, as their demand is relatively low.
The heat treatment of aluminum extrusions determines their mechanical properties, strength, and suitability for specific applications. Among the various heat treatment methods, T5, T6, and T66 are the most commonly used. Here’s an in-depth look:
Heat Treatment State | Cooling Method | Strength | Key Features and Benefits | Applications |
---|---|---|---|---|
T5 | Air cooling (fan) | Moderate | Adequate strength, good dimensional stability, used for architectural purposes. | Windows, doors, curtain walls, building structures. |
T6 | Water quenching (fast) | High | Higher strength and hardness, ideal for industrial and structural uses. | Automotive, aerospace, machinery, transport parts. |
T66 | Water quenching (fast) | Very high | Optimized mechanical properties for higher strength and performance demands. | Automotive, rail transportation, high-end machinery. |
Other Heat Treatment States
- T4: Solution heat-treated and naturally aged. Used in applications requiring intermediate strength and enhanced formability.
- T7: Overaged for better stress-corrosion resistance, often used for aerospace and marine purposes.
- O (Annealed): Very soft condition suitable for extensive forming or bending requirements.
- F (As-Fabricated): No heat treatment applied, used in non-critical applications with low strength requirements.
We provide a wide range of machining services for aluminum extrusions to meet specific requirements. These include cutting off/section removal, slotting, drilling holes, tapping threads, bending, and localized stamping to create deformations. For example, we can trim extruded profiles to custom lengths, mill precise grooves, create threaded holes for fasteners, bend profiles into specific shapes, or apply localized stamping to achieve custom forms or deformation.
In addition to these processes, we also offer TIG/MIG welding to join aluminum components for a solid structure. Furthermore, our services include assembly of common accessories, such as brackets, corner connectors, screws, hinges, end caps, and rubber seals, providing complete and ready-to-install profile solutions tailored to your project needs. This ensures that we can handle everything from simple cuts to highly customized fabrication and assembly, all with precision and efficiency.
For custom aluminum extrusion projects, we accept a variety of drawing formats, including CAD files, STEP files, and PDF files. However, for extrusions that require additional machining processes, it’s recommended to provide STEP files, as they ensure precise 3D modeling for machining accuracy.
While PDF files are acceptable, converting them into CAD drawings may result in the loss of certain details, requiring us to manually redraw the design, which could increase lead time. For the fastest and most accurate quotation, we recommend providing CAD files (e.g., DWG/DXF) and STEP files to ensure efficient design evaluation and pricing.
Mold fees are an essential part of the custom aluminum extrusion process. Since every order requires a uniquely designed mold tailored to specific requirements, these molds cannot be used for other products. Therefore, the mold fee is necessary and non-negotiable.
We require 100% upfront payment of the mold fee before mold development begins to ensure timely production. However, as a token of appreciation for your support, we offer a refund of the mold fee or equivalent discounts once the order reaches a certain production volume. Specific policies can be discussed based on your order volume and collaboration details.
Our minimum order quantity (MOQ) varies depending on the size of the product. For smaller-sized products, the MOQ is typically 500kg, while for larger-sized products, it is 2 tons.
We will specify the exact MOQ requirements during the quotation process. If your order quantity does not meet the MOQ, we can still arrange production, but an additional fee will be applied to cover mold preheating and production setup time. Rest assured, this extra fee will be reasonable, and we aim to keep it as minimal as possible to ensure smooth cooperation.
Packaging can be customized according to your needs. Options include using protective film or paper to separate and protect the surface, or foam film for additional surface protection. Products can be palletized or packed into cartons, and the quantity per pallet or carton can be specified by the customer.
The standard packaging involves bundling several pieces together with plastic wrap and then securing them onto pallets. Any packaging requirements beyond the standard will be accommodated, and the associated costs will be clearly provided to the customer.
Mold production typically takes 7 days. After the sample is confirmed, producing a full container load of 26 tons generally requires 14 days for extrusion alone. If surface treatment is required, an additional 3 days will be needed. For machining, extra time will be required depending on the complexity and volume of the machining work. The exact additional time for machining will be determined based on the specific processing requirements.
Hard anodizing significantly enhances the corrosion resistance of aluminum by forming a thick oxide layer, typically ranging from 25 to 150 microns in thickness, depending on the application. This dense and durable layer offers exceptional protection against moisture, chemicals, and saline environments, well beyond the capabilities of untreated aluminum. In salt spray tests, hard anodized aluminum has demonstrated the ability to resist corrosion for up to 1,000 hours or more, ensuring excellent performance in demanding applications. With proper maintenance, hard anodized aluminum profiles can last for 30-50 years or more, even in harsh environments, providing superior durability and long-term reliability.
The price of hard anodized aluminum profiles is determined by several factors, including raw material costs, extrusion processing fees, hard anodizing costs, and additional machining or packaging fees. While the cost of aluminum as a raw material fluctuates based on market conditions, the processing fees remain relatively stable. It is important to note that the hard anodizing process is more expensive than standard anodizing, typically costing 30-50% more, due to its thicker oxide layer (25-150 microns) and the additional time and precision required in the process.
Pricing can be calculated based on different methods depending on the profile’s specifications and requirements. For example, it can be calculated per weight (e.g., per ton), per length (e.g., per meter), or per piece, especially for profiles with extensive machining or custom designs.
We can manufacture aluminum profiles in compliance with technical requirements that meet European standards (EN), American standards (ASTM/AA), or other standards as specified by the customer. Custom production is tailored to ensure that the profiles meet the specific standard requirements requested.
Our production equipment is designed for the metric system. If the drawings provided are in the imperial system, we will convert them into metric units for production to ensure accuracy.
It is important to note that while we can machine imperial-threaded holes for fasteners, if you require us to supply matching imperial fasteners, they may not always be available in stock. Custom orders for imperial fasteners typically require a large volume for production. Please consider this when planning your project.
The majority of aluminum profiles we produce are custom-made and do not have existing molds. However, for some standard profiles such as square tubes, round tubes, U-channels, and T-SLOT profiles, we do have existing molds, and in some cases, small quantities in stock.
For certain specialized profiles, like ladder aluminum profiles, we have some molds that may be used across similar designs. For curtain wall and window/door profiles, we have developed a number of molds, though most are tailored to the Chinese domestic market.
Additionally, for furniture-related profiles, such as cabinet handles, cabinet door frames, skirting boards, tile edge trims, wall panel trims, stair anti-slip strips, partition aluminum profiles, corrugated aluminum profile (like long-span profiles), LED light channels, and photovoltaic frame supports, we offer a selection of ready-made designs and some existing molds.
We do not keep stock of hard anodized aluminum profiles due to their customized nature and the specific requirements of the hard anodizing process. For inquiries, we recommend contacting our sales team to discuss your project requirements, production timelines, and to receive further assistance.