Aluminum Cable Ladder Profile
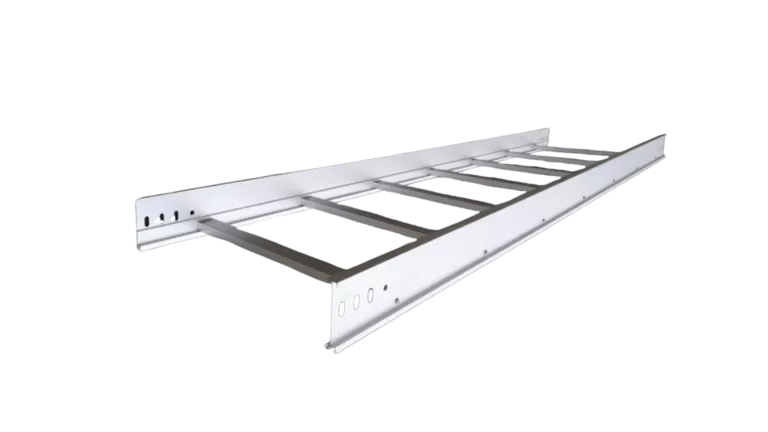
An aluminum cable ladder is an open-frame structure made primarily of high-strength aluminum alloy, designed to support and manage cables. Its main structure consists of side rails on both sides and rungs in the middle. Thanks to its characteristics of being lightweight, highly corrosion-resistant, strong, and easy to install, aluminum cable ladders are widely used in industries such as power, telecommunications, transportation, petrochemicals, construction, and data centers.
HTS-ALU is a professional aluminum profile manufacturer. In addition to aluminum extrusion, we provide services like punching, welding, machining, and anodizing to meet various customer requirements.
Aluminum Cable Ladder Side Rails
The main framework on both sides, responsible for supporting the rungs and the weight of the cables while determining the overall load-bearing capacity of the ladder.
Common designs include C-shaped, U-shaped, or profiles with reinforcing ribs to further enhance strength.
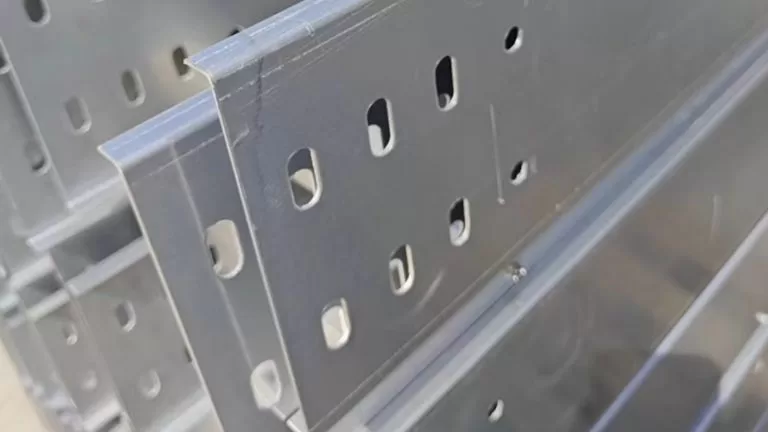
Aluminum Cable Ladder Rungs
Positioned between the side rails and arranged at regular intervals to support the cables.
The design of the rungs can vary, with options such as round, flat, or perforated shapes, balancing the need for load capacity and cable fixation.
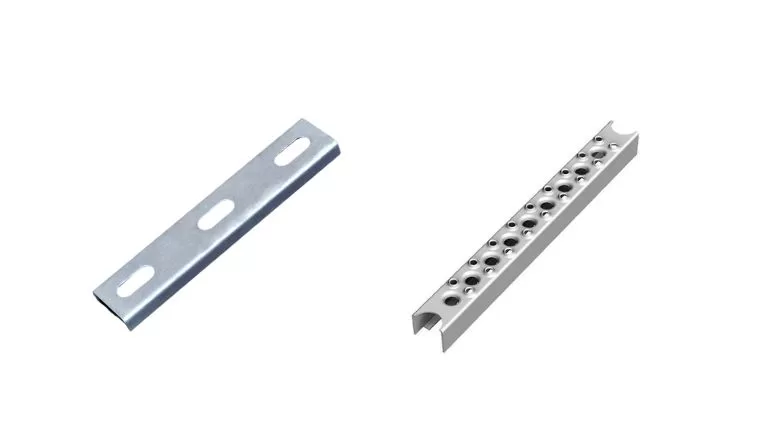
Common Specifications of Aluminum Cable Ladder
Width
150mm ~ 900mm, selected based on the quantity and diameter of the cables to be supported.
Height
Side Rail Height: Typically ranges from 50mm to 200mm, chosen according to the cable load-carrying requirements.
Rung Spacing
Generally set between 100mm and 300mm, determined by the specific application and cable support needs.
Length
Standard lengths range from 2 meters to 6 meters, with custom cutting available to meet project requirements.
Thickness
Based on load demand, the thickness of the side rails and rungs typically falls between 2mm and 5mm.
Material
Made from 6061-T6 aluminum alloy, ensuring high strength, durability, and corrosion resistance.
Surface Treatment Options
To enhance durability and aesthetics, aluminum cable ladders can undergo the following treatments:
Anodizing
- Improves corrosion resistance and allows for color options such as silver, black, gold, etc.
- Results in a smoother surface for easier cleaning and maintenance.
Electrostatic Powder Coating
- Enhances decorative appeal with a wider range of colors.
- Strengthens resistance to oxidation and abrasions.
Brushing or Polishing
- Enhances the metallic texture, making it ideal for high-end decorative purposes.
Building Aluminum Cable Ladders with T-Slot Profiles
Using T-slot aluminum profiles to construct aluminum cable ladders offers excellent modularity and versatility. The T-slot system allows for easy assembly, disassembly, and adjustments without requiring specialized tools. As a result, cable ladders can be customized to meet diverse project requirements, such as specific lengths, widths, and shapes to accommodate cables efficiently.
The T-slot grooves provide a secure framework to connect side rails and rungs with standard fasteners. Accessories like brackets, joints, and end caps can also be incorporated seamlessly to create custom solutions such as turns, branches, and multi-layer cable management systems. This approach is ideal for environments that demand flexibility, durability, and fast installation, such as industrial plants, data centers, and marine engineering projects.
Our Factory
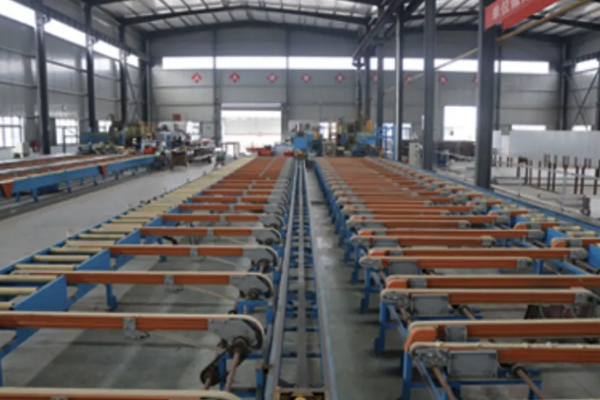
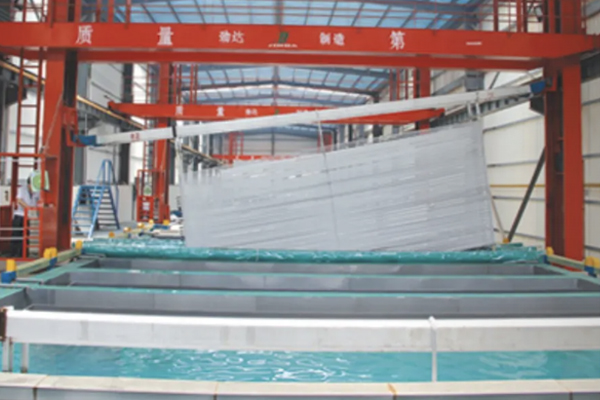
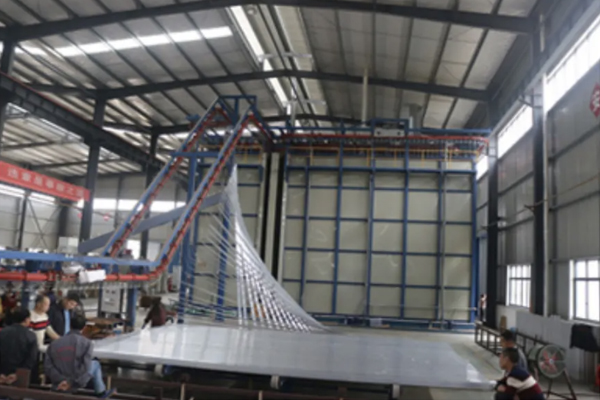
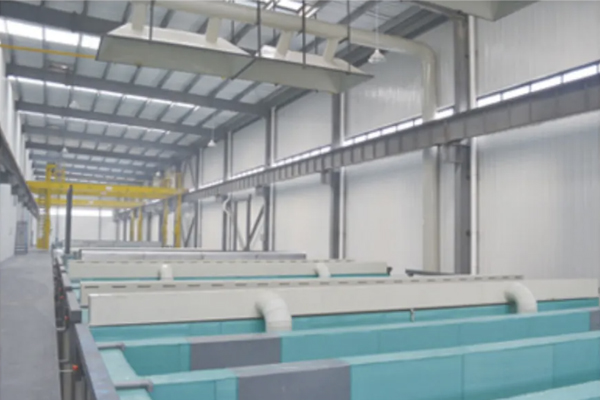
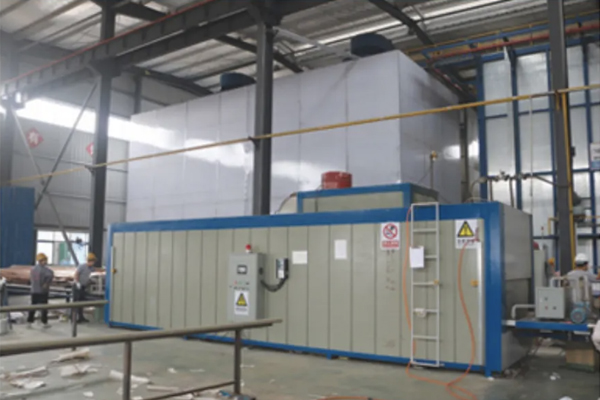
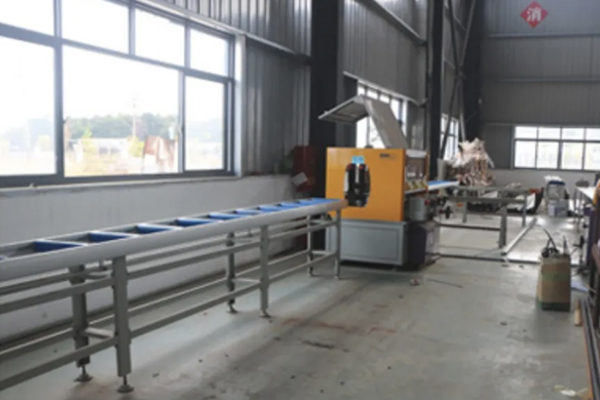
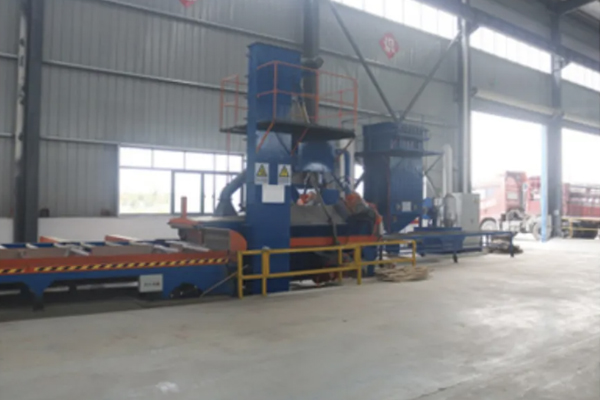
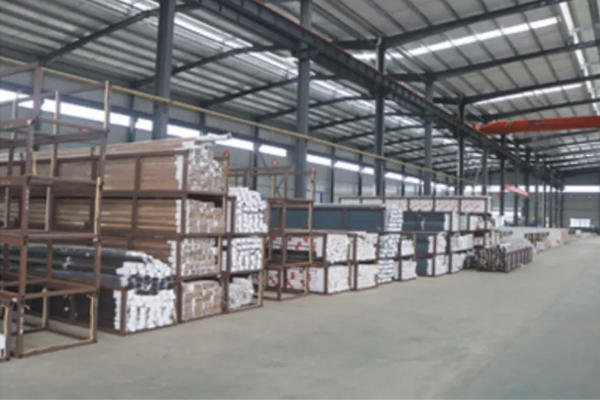
Custom Extrusion from Us
At HTS NEW MATERIALS, we specialize in providing custom aluminum extrusions designed to meet your unique requirements. With advanced production facilities and over 40 extrusion lines, we deliver premium, precision-engineered profiles for a wide range of industries, including aerospace, automotive, construction, and more.
Our custom extrusion services include:
- Tailored Cross-Sections: Create unique aluminum profiles with our expert die-making capabilities, customized to suit your specific project needs.
- Diverse Surface Finishes: Enhance both the appearance and durability of your profiles with options like anodizing, powder coating, polishing, and more.
- Precision Machining: Ensure exact dimensional accuracy with cutting, drilling, milling, and advanced machining services.
- Flexible Tempers: Select from a variety of heat treatments, including T5, T6, and others, to achieve the ideal mechanical properties for your application.
Partner with HTS NEW MATERIALS for innovative, cost-effective, and dependable custom aluminum extrusion solutions that drive the success of your project.
RFQ of Extruded Aluminum Profile
Industrial Environments
- Used in cable management systems for supporting and organizing power distribution cables and industrial equipment wiring.
- Commonly applied in chemical plants, power plants, refineries, and manufacturing facilities.
Telecommunications and Data Centers
- Ideal for laying fiber optics, telecommunication cables, and network lines, especially in environments requiring high heat dissipation and aesthetic appeal.
- Open-frame aluminum ladders effectively reduce the risk of cable overheating and simplify maintenance operations.
Construction and Infrastructure
- Used for indoor cable management in venues such as commercial buildings, shopping malls, airports, metro stations, and more.
- Aluminum ladders offer strong aesthetic integration with architectural designs.
Petrochemical and Energy Industries
- Coastal Areas: Aluminum ladders are the preferred choice due to their excellent corrosion resistance in high-salt environments.
- Oil & Gas Terminals: Easy installation and outstanding resistance to corrosion make them suitable for remote sites with limited maintenance resources.
Marine Engineering
- Widely used in ships, drilling platforms, and other offshore facilities.
- Aluminum’s lightweight and corrosion-resistant properties make it a perfect match for the demands of these environments.
Identify the Usage Environment
- Humid or Corrosive Environments? → Opt for aluminum with specialized treatments, such as anodizing, to enhance corrosion resistance.
- High Aesthetic Requirements? → Prioritize options with polished or powder-coated finishes for a premium appearance.
Determine Load Requirements
- Select the appropriate width, thickness, and load-bearing strength based on the type and quantity of cables.
- For extremely heavy loads, consider using side rails with reinforcing ribs or increasing the number of rungs.
Design and Installation Flexibility
- Need intricate layouts with turns or branches? → Pair the ladder with functional accessories like T-joints, elbows, and other connectors to suit on-site requirements.
Consider the Budget
- While aluminum ladders are relatively more expensive than steel, their maintenance-free characteristics lead to lower lifecycle costs.
- Ideal for projects with tight budgets but high service expectations due to their durability and long-term cost-effectiveness.
The primary aluminum alloys used for extrusion belong to the 6xxx series, specifically 6061, 6063, 6060,6082 and 6066. These alloys are highly favored due to their excellent extrudability, good mechanical properties, and corrosion resistance.
- 6061: A versatile alloy with higher strength, suitable for structural and transportation applications.
- 6063: Known as the “architectural alloy,” it offers excellent surface finish and is widely used for decorative and structural purposes.
- 6060: Similar to 6063 but with slightly lower strength, ideal for intricate and thin-walled profiles.
- 6066: A high-strength alloy within the 6xxx series, often used in more demanding structural applications.
- 6082: A strong alloy with better mechanical properties compared to 6061 and excellent corrosion resistance, commonly used in high-load structural applications and in marine environments.
The 7xxx series alloys, such as 7075, are used in applications requiring extremely high strength and performance, such as aerospace and high-end engineering projects. However, they have lower corrosion resistance when compared to 6xxx alloys and are therefore less commonly used for general extrusion applications.
While 1xxx, 3xxx, and 5xxx series alloys can be extruded, they are generally used infrequently for extrusion due to their lower strength or other limitations compared to 6xxx and 7xxx alloys. These series are mainly used in specialized applications. Additionally, if extrusion products from these series are requested, higher minimum order quantities (MOQ) are typically required for custom production, as their demand is relatively low.
We provide a wide range of machining services for aluminum extrusions to meet specific requirements. These include cutting off/section removal, slotting, drilling holes, tapping threads, bending, and localized stamping to create deformations. For example, we can trim extruded profiles to custom lengths, mill precise grooves, create threaded holes for fasteners, bend profiles into specific shapes, or apply localized stamping to achieve custom forms or deformation.
In addition to these processes, we also offer TIG/MIG welding to join aluminum components for a solid structure. Furthermore, our services include assembly of common accessories, such as brackets, corner connectors, screws, hinges, end caps, and rubber seals, providing complete and ready-to-install profile solutions tailored to your project needs. This ensures that we can handle everything from simple cuts to highly customized fabrication and assembly, all with precision and efficiency.
For custom aluminum extrusion projects, we accept a variety of drawing formats, including CAD files, STEP files, and PDF files. However, for extrusions that require additional machining processes, it’s recommended to provide STEP files, as they ensure precise 3D modeling for machining accuracy.
While PDF files are acceptable, converting them into CAD drawings may result in the loss of certain details, requiring us to manually redraw the design, which could increase lead time. For the fastest and most accurate quotation, we recommend providing CAD files (e.g., DWG/DXF) and STEP files to ensure efficient design evaluation and pricing.
Mold fees are an essential part of the custom aluminum extrusion process. Since every order requires a uniquely designed mold tailored to specific requirements, these molds cannot be used for other products. Therefore, the mold fee is necessary and non-negotiable.
We require 100% upfront payment of the mold fee before mold development begins to ensure timely production. However, as a token of appreciation for your support, we offer a refund of the mold fee or equivalent discounts once the order reaches a certain production volume. Specific policies can be discussed based on your order volume and collaboration details.
Our minimum order quantity (MOQ) varies depending on the size of the product. For smaller-sized products, the MOQ is typically 500kg, while for larger-sized products, it is 2 tons.
We will specify the exact MOQ requirements during the quotation process. If your order quantity does not meet the MOQ, we can still arrange production, but an additional fee will be applied to cover mold preheating and production setup time. Rest assured, this extra fee will be reasonable, and we aim to keep it as minimal as possible to ensure smooth cooperation.
Packaging can be customized according to your needs. Options include using protective film or paper to separate and protect the surface, or foam film for additional surface protection. Products can be palletized or packed into cartons, and the quantity per pallet or carton can be specified by the customer.
The standard packaging involves bundling several pieces together with plastic wrap and then securing them onto pallets. Any packaging requirements beyond the standard will be accommodated, and the associated costs will be clearly provided to the customer.
Mold production typically takes 7 days. After the sample is confirmed, producing a full container load of 26 tons generally requires 14 days for extrusion alone. If surface treatment is required, an additional 3 days will be needed. For machining, extra time will be required depending on the complexity and volume of the machining work. The exact additional time for machining will be determined based on the specific processing requirements.
Aluminum profiles are naturally corrosion-resistant due to the formation of a thin, protective oxide layer when exposed to air or water. This oxide layer is stable and self-repairing, meaning that even if the surface is scratched or cut (such as at exposed ends or during processing), the aluminum will not rust or corrode like iron or steel. Instead, the exposed areas will quickly form a new oxide layer, providing continuous protection against further oxidation.
With proper design, installation, and maintenance, aluminum profiles can last for decades, even in challenging environments. For example, untreated aluminum can easily withstand 20-30 years in outdoor applications, while profiles with surface treatments like anodizing or powder coating can last even longer, often exceeding 50 years. This makes aluminum an excellent choice for applications where durability and long-term performance are essential.
The price of aluminum profiles consists of several components: raw material costs, extrusion processing fees, surface treatment fees, machining costs, and additional packaging fees. Among these, the cost of aluminum as a raw material tends to fluctuate frequently, while other fees remain relatively stable. Due to these fluctuations, our quotations are typically valid for 7 days.
Pricing can be structured in different ways depending on the product and requirements. It can be calculated by weight (e.g., cost per ton), by length (e.g., cost per meter), or by piece (e.g., cost per unit). For products involving extensive machining, such as heat sinks, pricing is generally calculated on a per-piece basis to accurately reflect the additional processing costs. This flexible pricing approach ensures the quote is tailored to the specific needs of the customer.
We can manufacture aluminum profiles in compliance with technical requirements that meet European standards (EN), American standards (ASTM/AA), or other standards as specified by the customer. Custom production is tailored to ensure that the profiles meet the specific standard requirements requested.
Our production equipment is designed for the metric system. If the drawings provided are in the imperial system, we will convert them into metric units for production to ensure accuracy.
It is important to note that while we can machine imperial-threaded holes for fasteners, if you require us to supply matching imperial fasteners, they may not always be available in stock. Custom orders for imperial fasteners typically require a large volume for production. Please consider this when planning your project.