Comparison of Corrosion Resistance in Different Surface Treatments of Aluminum Profiles
Aluminum profiles are widely used in construction, industrial manufacturing, and aerospace due to their lightweight, high strength, durability, and excellent machinability. However, the surface of aluminum is prone to reacting with air, moisture, and other elements, leading to oxidation or corrosion. Surface treatment plays a critical role in enhancing the corrosion resistance, aesthetic quality, and functional properties of aluminum profiles.
This article explores common surface treatment techniques for aluminum profiles and compares their corrosion resistance, helping users select the most suitable solution for various applications.
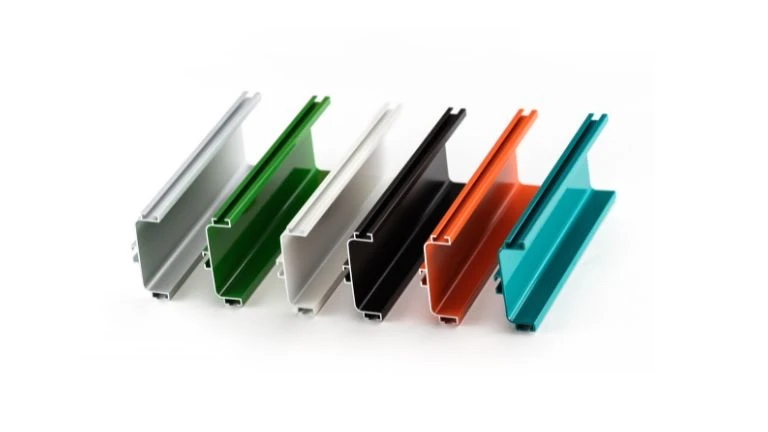
I. Common Surface Treatment Methods for Aluminum Profiles
-
Anodizing Anodizing is an electrochemical process that forms a protective oxide layer on the aluminum surface. This oxide layer, composed of aluminum oxide, is hard and dense, offering excellent protection against corrosion.
Features:
- Significantly enhances corrosion resistance, especially in acidic or alkaline environments.
- Provides strong adhesion for coloring and further coatings.
- Offers a variety of finishes, such as matte, brushed, or shiny textures.
-
Powder Coating Powder coating involves applying a uniform layer of powder paint to the aluminum surface, followed by heating to cure the paint into a protective and aesthetic coating.
Features:
- Offers a thick, even coating that is highly resistant to corrosion, making it well-suited for humid and saline environments.
- Provides a wide range of color options, ideal for decorative purposes.
- Excellent wear and impact resistance; however, overly thick coatings may crack or peel over time.
-
Electrophoretic Coating Electrophoretic coating uses an electrical field to uniformly deposit paint particles onto the aluminum surface, forming a dense protective layer.
Features:
- Produces an even, dense coating with superior corrosion resistance compared to general paint or powder coating.
- Offers smooth finishes with a glossy, transparent appearance, ideal for high-end aluminum applications.
- Excellent adhesion and weather resistance, suitable for outdoor use.
-
Polishing (Mechanical/Chemical) Polishing removes surface irregularities to achieve a smooth and shiny finish, either through mechanical or chemical means. While primarily aesthetic, it can complement other protective treatments.
Features:
- Minimal improvement in corrosion resistance unless combined with additional treatments such as anodizing or coating.
- Primarily used to enhance visual appeal.
-
PVDF Coating (Fluorocarbon Coating) PVDF coating applies fluorocarbon resin-based paint to form a highly durable layer with outstanding corrosion and weather resistance.
Features:
- Exceptional protection against corrosion and UV radiation, making it ideal for extremely harsh environments.
- Long-lasting performance, especially suitable for high-rise building exteriors.
- Higher cost and requires precise application procedures.
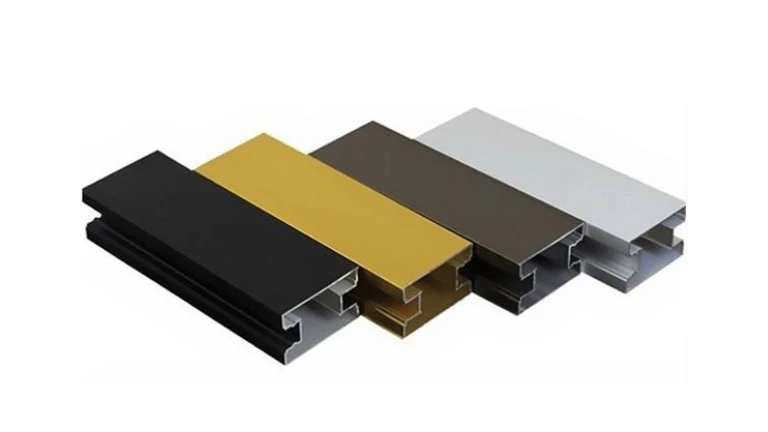
II. Corrosion Resistance Comparison
The table below compares the corrosion resistance and other key characteristics of these surface treatments:
Treatment Method | Corrosion Resistance | Oxidation Resistance | Weather Resistance | Suitable Applications |
---|---|---|---|---|
Anodizing | ★★★★☆ | ★★★★★ | ★★★★☆ | Indoor and general outdoor use |
Powder Coating | ★★★★☆ | ★★★★☆ | ★★★★☆ | Humid and saline environments |
Electrophoretic Coating | ★★★★★ | ★★★★★ | ★★★★☆ | High-end and outdoor use |
PVDF Coating | ★★★★★ | ★★★★★ | ★★★★★ | Extreme climates and UV exposure |
Polishing | ★★★☆☆ | ★★★☆☆ | ★★☆☆☆ | Indoor decorative use |
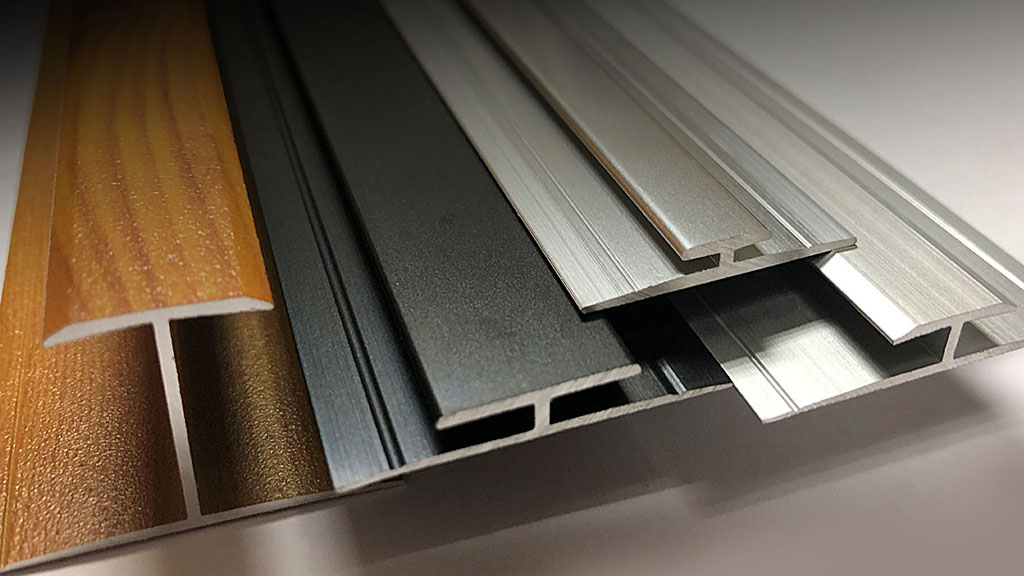
III. Recommendations for Different Use Cases
Indoor Decoration:
- Preferred treatments: Anodizing, Electrophoretic Coating.
- These methods provide high aesthetic value with good corrosion resistance for environments with minimal exposure to moisture or extreme temperatures.
Humid and Coastal Environments:
- Preferred treatments: Powder Coating, PVDF Coating.
- These techniques offer superior protection against moisture and salt-induced corrosion.
Building Facades and Curtain Walls:
- Preferred treatments: PVDF Coating, Electrophoretic Coating.
- PVDF coatings excel in extreme weather and UV conditions, while electrophoretic coatings combine aesthetics with durability for premium applications.
Industrial Applications:
- Preferred treatment: Anodizing.
- The robust oxide layer formed through anodizing provides chemical and wear resistance, making it suitable for demanding industrial environments.
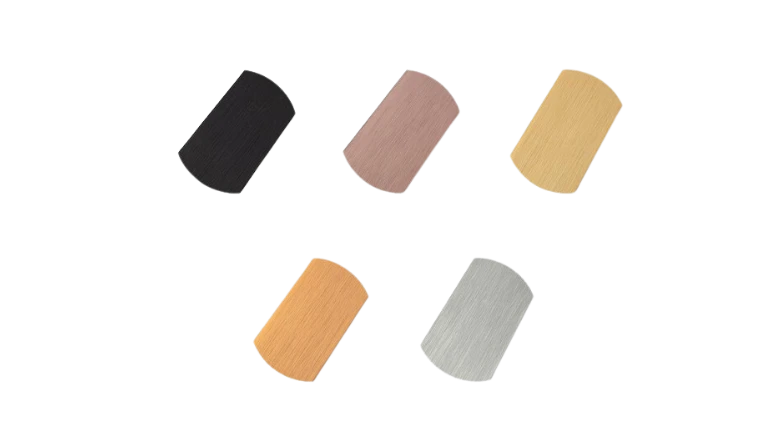
IV. Cost-Performance Considerations
The choice of a surface treatment is often a balance between performance and cost:
- Cost-effective options: Anodizing and Powder Coating.
- Mid-range option: Electrophoretic Coating.
- High-end option: PVDF Coating (best performance for demanding environments).
By carefully considering the corrosion environments, durability requirements, and budget constraints, users can select a treatment method that provides optimal protection and value.
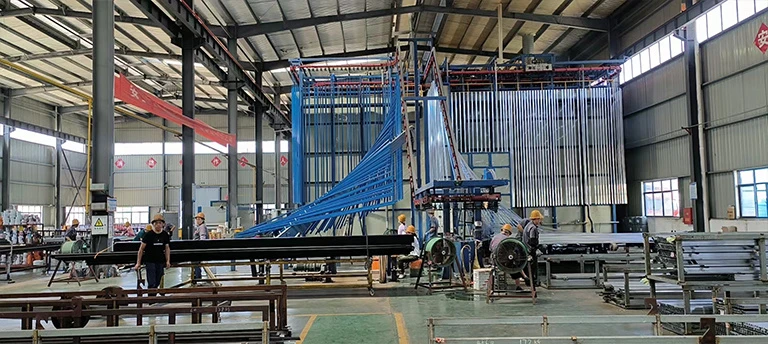
V. Summary
Surface corrosion not only compromises the longevity of aluminum profiles but also affects their aesthetic and functional properties. Surface treatment techniques—such as anodizing, powder coating, electrophoretic coating, and PVDF coating—offer different levels of protection against corrosion, weather, and UV exposure.
For moderate environments, anodizing and electrophoretic coatings offer excellent value and balanced performance. Meanwhile, powder coating is preferred in mild but high-humidity areas. For harsh outdoor or industrial applications, PVDF coating is the gold standard, albeit at a higher cost.
By understanding the benefits and limitations of each surface treatment, users can make informed decisions to ensure the long-lasting performance and appearance of aluminum profiles.
Custom Your Aluminum Profile
Our aluminum extrusion factory, located in Nanchang, Jiangxi Province, covers an extensive area of 30,000 square meters and is home to a dedicated workforce of over 120 skilled individuals.
Advanced Extrusion Lines
Boasting over 30 high-precision extrusion production lines from Japan and Germany, we ensure unmatched quality and efficiency.
Custom Mold Design and Processing
We tailor-make molds based on client designs or samples, providing prototypes for confirmation to meet precise specifications.
Comprehensive Surface Treatment Techniques
Our surface treatment capabilities include anodizing, electroplating, sandblasting, powder coating, fluorocarbon painting, and wood grain transfer printing to enhance product durability and aesthetics.
Over Two Decades of Expertise
Since 2013, we have been manufacturing aluminum profiles, accumulating vast experience in producing a wide array of profiles for windows, doors, and various industrial applications.
Aluminium Profile Solutions
At HTS Aluminium, we pride ourselves on our ability to deliver custom aluminium profile solutions tailored to the unique needs of each client. Our bespoke services are grounded in a deep understanding of our clients’ visions, which we bring to life by transforming drawings or samples into precision-engineered aluminium profiles.
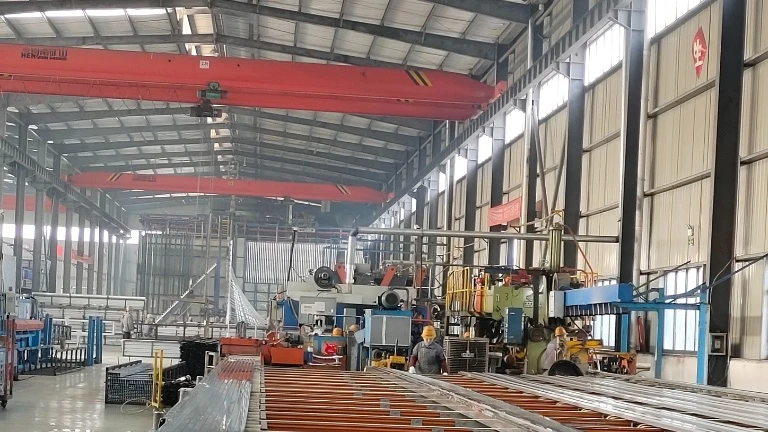
Precision Aluminum Extrusion Process
Our state-of-the-art manufacturing facility is equipped with advanced extrusion presses and precision cutting tools, allowing us to handle even the most complex profiles with exceptional accuracy. Our team of skilled technicians brings years of industry experience to the table, ensuring that every extruded aluminium profile meets the highest standards of quality and precision.
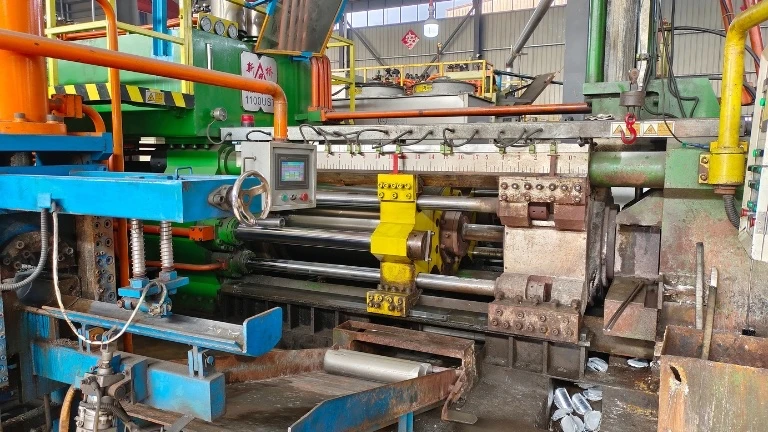
Design and Manufacture of Moulds
We at HTS Aluminium specialize in the design and manufacture of custom moulds based on client specifications. Once a mould is created, we conduct trial productions and send samples to our clients for confirmation. This meticulous process ensures that the final product perfectly aligns with our clients’ expectations.
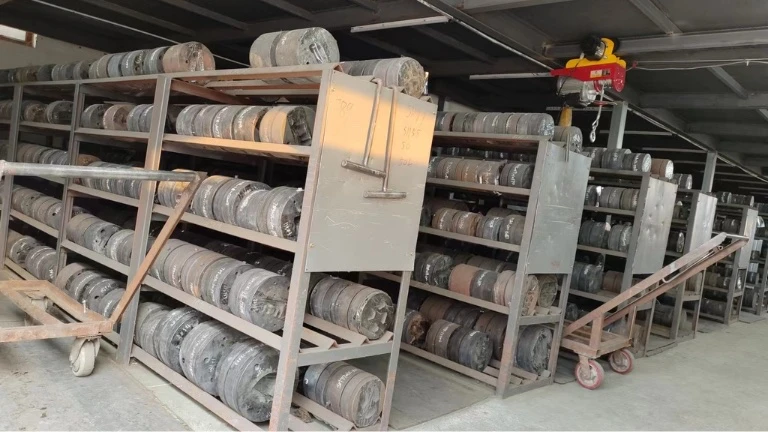
Material for Extruded Aluminum
Quality begins with the raw materials, and at HTS Aluminium, we use only the highest standard aluminium alloys for our extrusions. Our profiles are commonly crafted from a selection of industry-standard grades, each offering a balance of strength, durability, and corrosion resistance to meet various application requirements.
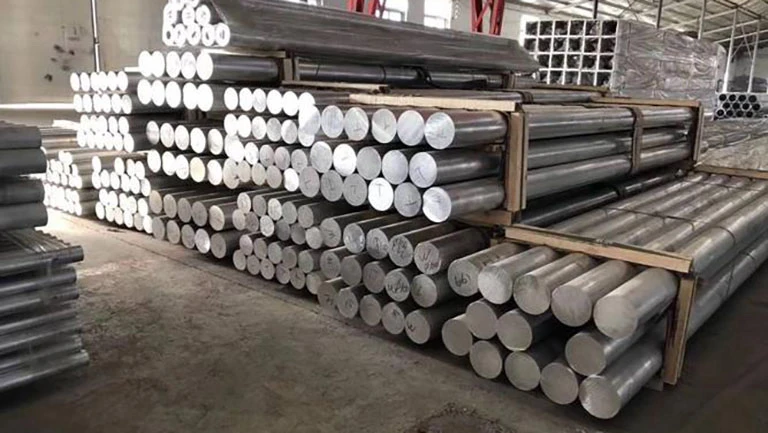
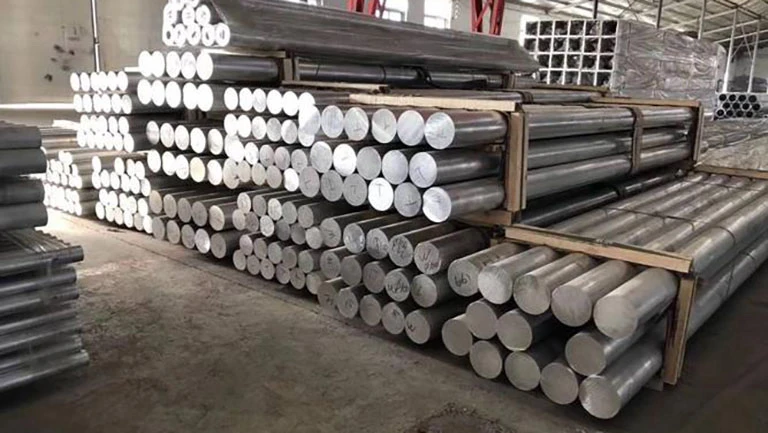
5052: Offers excellent corrosion resistance, good weldability, and moderate-to-high strength. It is a popular choice for marine and automotive applications.
Silicon (Si): 0.25% (Maximum)
Iron (Fe): 0.40% (Maximum)
Copper (Cu): 0.10% (Maximum)
Manganese (Mn): 0.10% (Maximum)
Magnesium (Mg): 2.2-2.8%
Chromium (Cr): 0.15-0.35%
Zinc (Zn): 0.10% (Maximum)
Remaining Balance: Aluminum (Al)
6061: A versatile alloy with good mechanical properties, weldability, and corrosion resistance. It is widely used for structural applications and in the automotive industry.
Silicon (Si): 0.40-0.80%
Iron (Fe): 0.70% (Maximum)
Copper (Cu): 0.15-0.40%
Manganese (Mn): 0.15% (Maximum)
Magnesium (Mg): 0.8-1.2%
Chromium (Cr): 0.04-0.35%
Zinc (Zn): 0.25% (Maximum)
Titanium (Ti): 0.15% (Maximum)
Remaining Balance: Aluminum (Al)
6063: Often referred to as an architectural alloy, it has a smooth surface finish and is commonly used in window and door frames.
Silicon (Si): 0.20-0.60%
Iron (Fe): 0.35% (Maximum)
Copper (Cu): 0.10% (Maximum)
Manganese (Mn): 0.10% (Maximum)
Magnesium (Mg): 0.45-0.90%
Chromium (Cr): 0.10% (Maximum)
Zinc (Zn): 0.10% (Maximum)
Titanium (Ti): 0.10% (Maximum)
Remaining Balance: Aluminum (Al)
7075: One of the strongest aluminum alloys available, with zinc as the main alloying element. It is used in applications where strength is critical, such as in aerospace and military components.
Zinc (Zn): 5.1-6.1%
Magnesium (Mg): 2.1-2.9%
Copper (Cu): 1.2-2.0%
Chromium (Cr): 0.18-0.28%
Silicon (Si): 0.40% (Maximum)
Iron (Fe): 0.50% (Maximum)
Manganese (Mn): 0.30% (Maximum)
Titanium (Ti): 0.20% (Maximum)
Other elements: Each 0.05% (Maximum), Total 0.15% (Maximum)
Remaining Balance: Aluminum (Al)
Heat Treatment Options
Our aluminium profiles can undergo a range of heat treatment options to enhance their properties. From T5 to T6 treatments, we tailor the process to achieve the desired level of hardness, strength, and elasticity. Each treatment option is designed to bring out the best in the material, ensuring that the final product stands up to the demands of its application.
T5 Heat Treatment
Process: Cooled from an elevated temperature shaping process and then artificially aged.
Characteristics: Increases the strength of the aluminum by accelerating the aging process, resulting in a material that has moderate strength and good formability.
T6 Heat Treatment
Process: Solution heat-treated and then artificially aged.
Characteristics: Provides a significant increase in strength compared to T5 by altering the microstructure of the aluminum. This results in a high-strength material with good machinability and fair formability.
Machine Process after Extrusion
At our factory, we offer a wide range of machining services to enhance the functionality of our aluminum profiles. Our capabilities include precision cutting for exact lengths, punching and threading for modifications, and slotting for component compatibility. We also specialize in bending and welding for complex assemblies and robust structures. Additionally, our assembly services ensure complete, ready-to-use components.
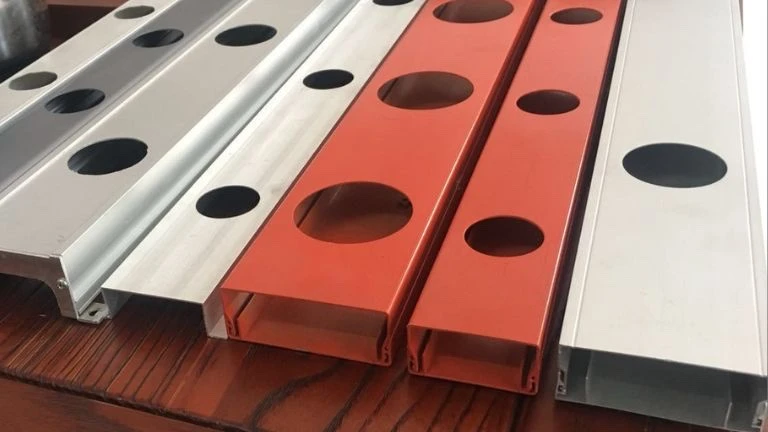
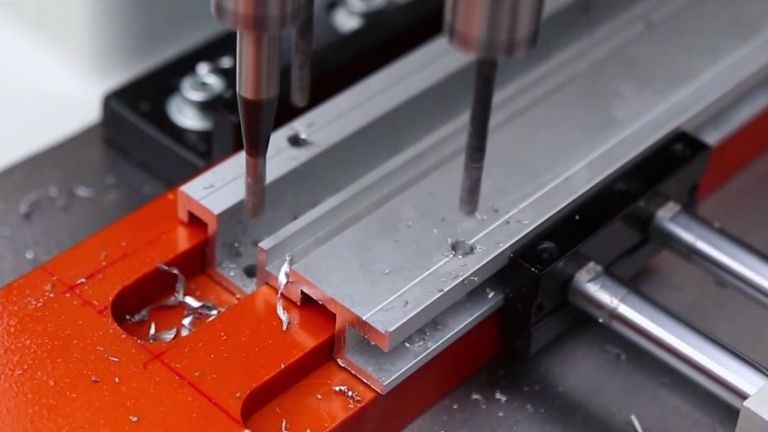
Punching
Punching, involves applying high force to create holes, indentations, or other shapes in aluminum profiles. This process is essential for creating ventilation openings, mounting slots, or lightweight structures with uniform patterns.
Drilling
Drilling creates necessary holes in aluminum profiles, allowing for the attachment of components with bolts or other fasteners, crucial for modular constructions.
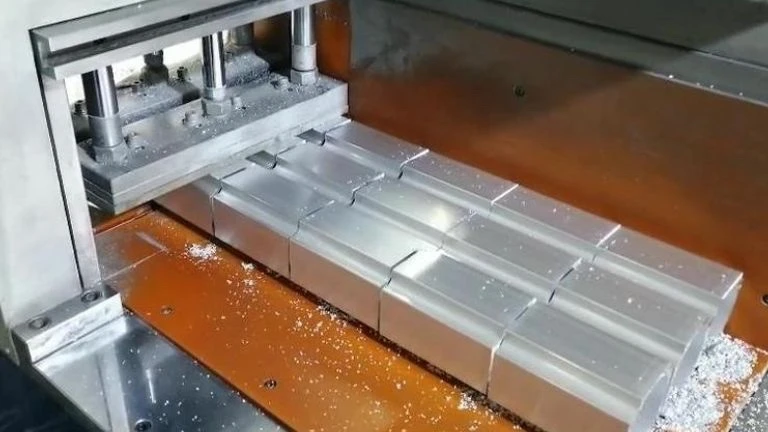
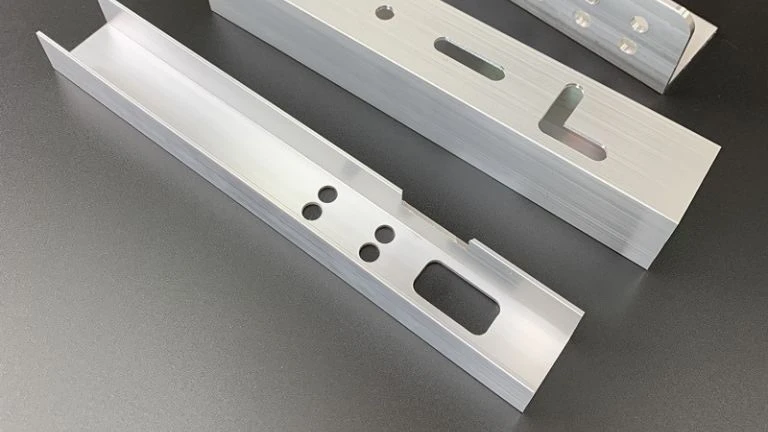
Cutting
Precision cutting is crucial to ensure that each aluminum profile is trimmed to exact length specifications, facilitating a perfect fit in final assembly.
Milling
Milling involves the removal of aluminum material using rotary cutters to achieve desired shapes and surfaces. This process is perfect for creating slots, grooves, and complex contours, enhancing the functionality and precision of aluminum profiles.
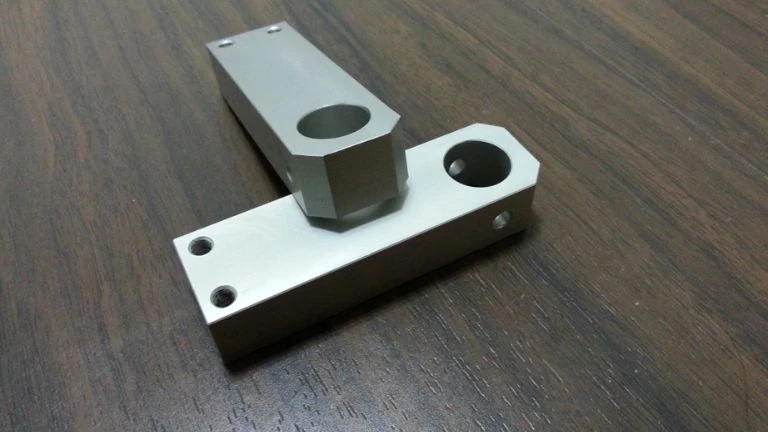
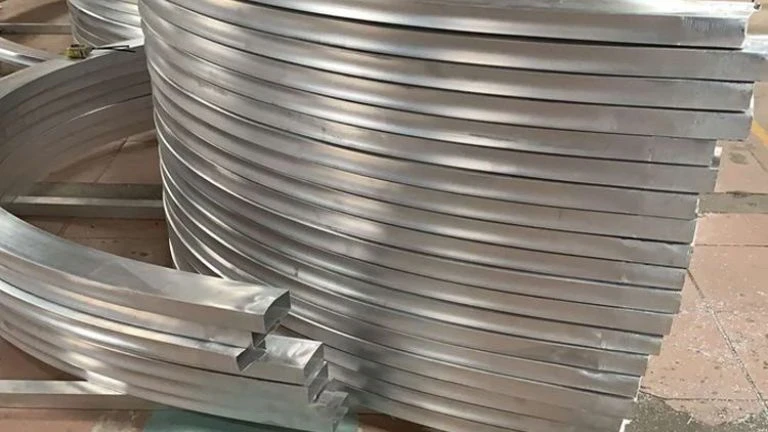
Tapping
Tapping adds threads to the drilled holes in aluminum profiles, enabling the secure fastening of bolts and screws, which is vital for assembly and maintenance.
This technique shapes aluminum profiles into desired curves or angles, maintaining material integrity and is essential for both architectural and functional structures.
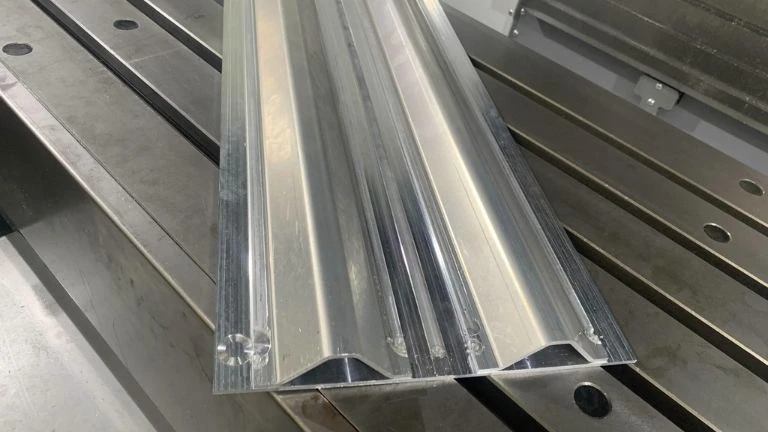
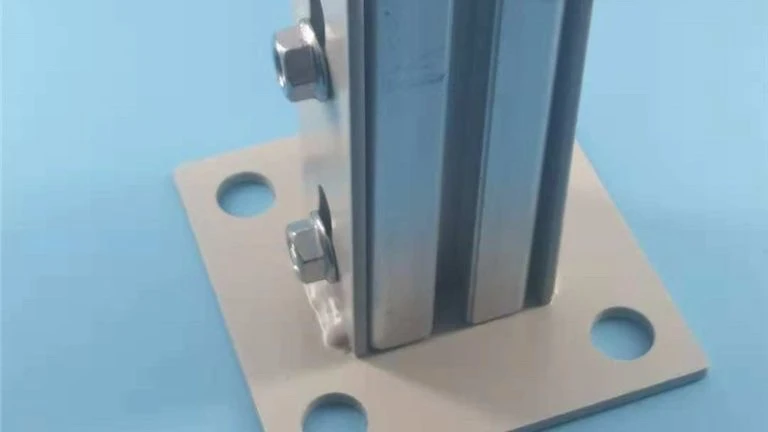
Welding
Welding joins multiple aluminum sections into a solid unit, providing a durable bond essential for structural applications.
Assembly
Our assembly services involve the strategic joining of various components using bolts and other fasteners to create complex assemblies, ensuring functionality and structural integrity.
Custom Aluminum Extrusion Process
At HTS Aluminum Profiles, we specialize in delivering custom aluminum extrusion solutions tailored to your specific needs. Here’s a step-by-step guide to our customization process:
Step 1: Initial Consultation
Your journey begins with an initial consultation where we discuss your project requirements. We encourage you to share your design concepts, application needs, and any critical parameters that the aluminum profile must meet. This collaborative approach ensures that we fully understand your vision and objectives.
Step 2: Design and Engineering
Leveraging our extensive experience in aluminum extrusion, our skilled engineers work closely with you to refine your design. We consider factors such as the aluminum alloy grade, temper, and mechanical properties required for your application. Our team uses advanced CAD software to create precise technical drawings and 3D models of the proposed profile.
Step 3: Die Fabrication
Once the design is finalized, we proceed to manufacture the custom extrusion dies. Our precision die-making process ensures that the final profile will match your specifications with high accuracy. We employ state-of-the-art CNC machines to craft dies that can withstand the rigors of extrusion while maintaining tight tolerances.
Step 4: Aluminum Extrusion
With the dies ready, the actual extrusion process begins. We select the appropriate aluminum alloy and heat it to the precise extrusion temperature. The heated billet is then pressed through the die to create the custom profile. Our extrusion presses, ranging from 600 to 3600 tons, are capable of producing a wide range of profile sizes and shapes.
Step 5: Surface Treatment and Finishing
Following extrusion, the profiles undergo various surface treatments as per your requirements. Options include anodizing, electroplating, sandblasting, powder coating, fluorocarbon painting, and wood grain transfer printing. These processes enhance the profiles’ durability, corrosion resistance, and aesthetic appeal.
Step 6: Quality Assurance
Quality is at the heart of everything we do. Each custom aluminum profile is subjected to rigorous quality checks to ensure it meets ISO standards and our European quality certifications. We perform dimensional inspections, mechanical testing, and surface finish evaluations to guarantee that your profiles are delivered without defects.
Step 7: Packing and Delivery
After passing all quality inspections, the aluminum profiles are carefully packed to prevent any damage during transit. We use robust packaging materials and methods tailored to the profiles’ dimensions and your delivery preferences. Our logistics team then manages the safe and timely delivery of your custom aluminum profiles to your specified location.
Step 8: After-Sales Support
Our commitment to your satisfaction extends beyond delivery. We offer comprehensive after-sales support to address any concerns or additional requirements you may have. Our customer service team is always ready to assist you with any questions or feedback.
Partner with Us
We are committed to delivering precision-engineered aluminum profiles that meet the highest standards of quality. From initial design to final delivery, we provide a seamless and personalized experience, ensuring that your custom aluminum solutions are produced efficiently and to your satisfaction.
Take the next step in your project and contact us for a consultation on your custom aluminum extrusion needs.