Will Aluminium Rust or Corrode?
In modern material science, the durability and longevity of metals are crucial. A common question is whether aluminium, a versatile metal, can rust. The answer is no; aluminium does not rust like iron. Instead, it forms a protective oxide layer that prevents further corrosion.
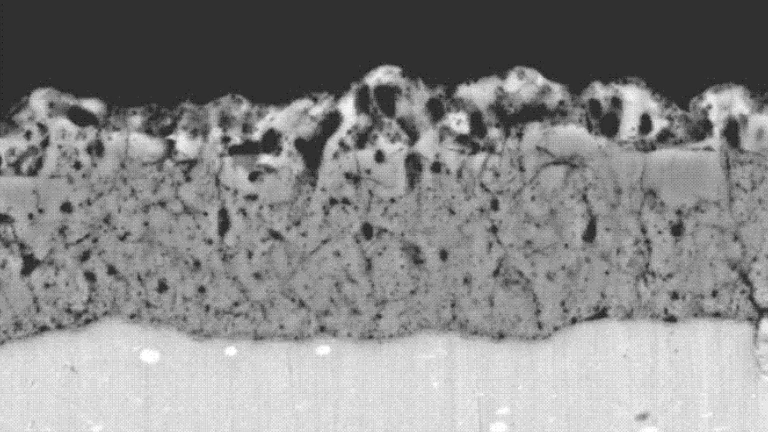
Rust Versus Corrosion
Rust and corrosion, though often used interchangeably, represent distinct phenomena. ‘Rust’ specifically refers to the oxidation of iron or steel, resulting in iron oxide, a red or brown crusty deposit. In contrast, ‘corrosion’ is a broader term that encompasses the deterioration of any metal due to a chemical reaction with its environment. Aluminium does not rust, as it lacks iron; however, it is not immune to corrosion. Aluminium corrosion manifests differently and under various conditions.
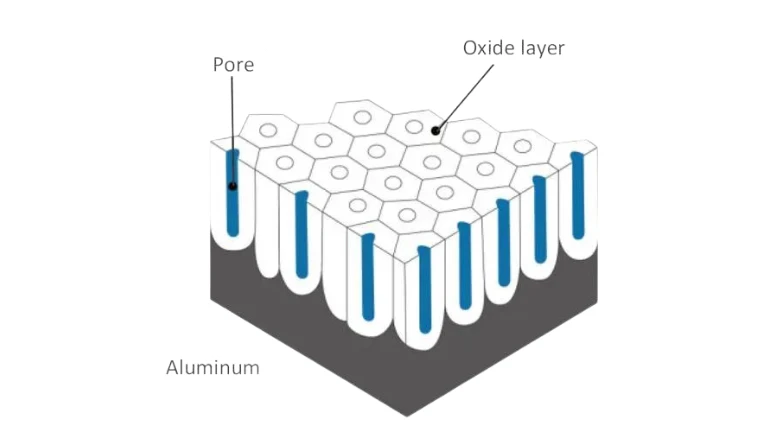
Aluminium’s Reaction with Air and Oxygen
Aluminium is widely used in outdoor applications such as windows, curtain walls, fences, and roofing sheets because of its exceptional resistance to corrosion. This resistance stems from its reaction with oxygen. When aluminium is exposed to air, it rapidly forms a thin, adherent layer of aluminium oxide (Al₂O₃). This oxide layer acts as a protective barrier, preventing further oxidation of the underlying metal. Unlike rust on iron, which flakes away and exposes fresh metal to corrosion, the aluminium oxide layer is stable, non-porous, and does not detach. Consequently, aluminium maintains its integrity and appearance under normal atmospheric conditions, making it ideal for outdoor use.
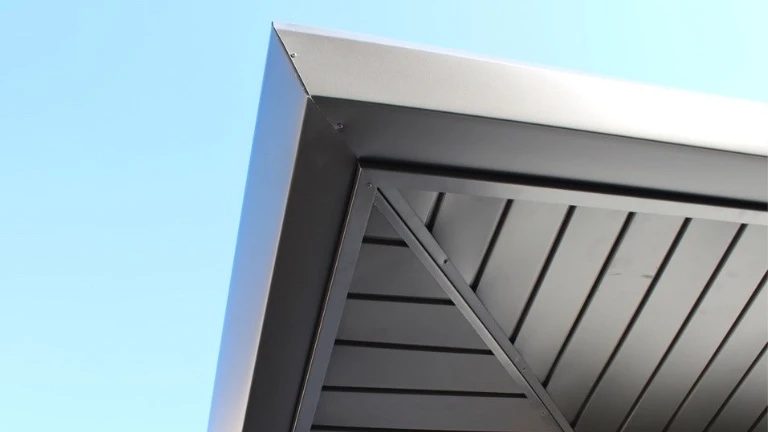
Impact of Humid Environments on Aluminium
In humid environments, aluminium forms a protective oxide layer more rapidly. However, prolonged exposure to moisture, especially with impurities like salts, can cause pitting corrosion—small, localized holes that may weaken the metal over time. To address this, protective coatings, regular maintenance, and corrosion-resistant aluminium alloys are effective solutions.
Interaction with Acids and Alkalis
Aluminium’s resistance to chemicals varies. It is highly reactive with strong acids and bases, which can disrupt the protective oxide layer and cause significant corrosion. For instance, aluminium readily dissolves in hydrochloric acid (HCl) and sodium hydroxide (NaOH), leading to rapid degradation. However, it shows considerable resistance in weak acids like citric acid. Thus, the chemical environment is crucial when using aluminium.
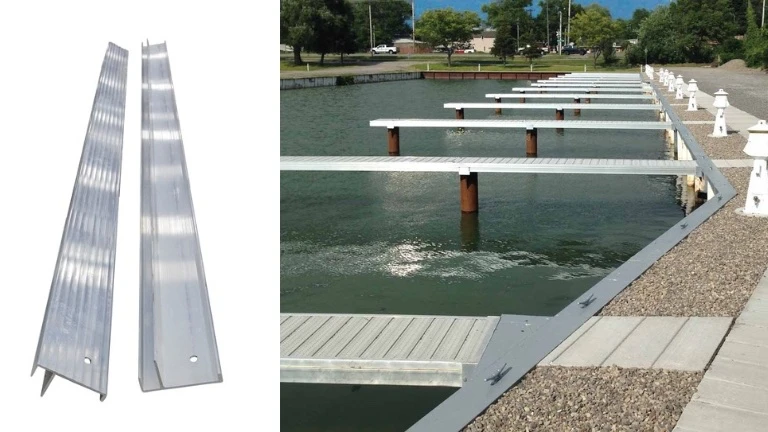
Exposure to Seawater
Seawater presents a significant challenge for aluminium due to its high chloride content, which promotes corrosion. Chlorides can disrupt the protective oxide layer, leading to localized issues such as pitting and intergranular corrosion. For marine applications, such as shipbuilding, it is crucial to use aluminium alloys that possess enhanced resistance to marine environments. Alloys like 5083 and 6061, which include elements like magnesium and silicon, are well-suited for this purpose due to their superior corrosion resistance.
Aluminum Alloys Corrosion Resistance
Aluminum has good inherent corrosion resistance due to a thin, protective oxide layer that forms naturally when exposed to air. However, alloying aluminum with other metals can alter its corrosion resistance. The 5xxx series, known for its high magnesium content, is often preferred for applications requiring excellent corrosion resistance, particularly in marine environments. In contrast, the 7xxx series, despite its high strength, is more susceptible to corrosion and is typically used only when its strength outweighs the corrosion risks, with protective measures in place.
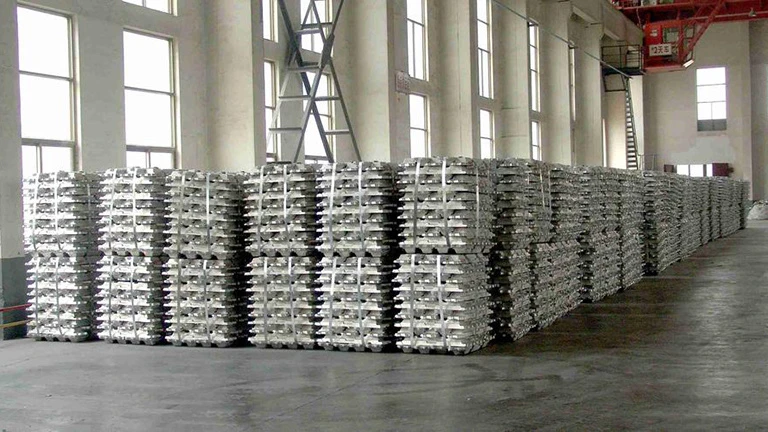
1xxx Series (Unalloyed, Pure Aluminum – e.g., 1100, 1200)
- Composition: Approximately 99% aluminum.
- Corrosion Resistance: Excellent due to the high purity of aluminum. However, it’s relatively low in strength compared to the alloyed versions.
- Common Applications: Chemical processing equipment, electrical applications, and some food industry components.
2xxx Series (Copper Alloys – e.g., 2024)
- Composition: Primarily aluminum and copper.
- Corrosion Resistance: Less resistant to corrosive environments, especially susceptible to intergranular corrosion. Often needs protective coatings or treatments.
- Common Applications: Aerospace and military applications where strength is critical, and protective measures against corrosion can be taken.
3xxx Series (Manganese Alloys – e.g., 3003)
- Composition: Aluminum and manganese.
- Corrosion Resistance: Good resistance to corrosive environments; better than pure aluminum but not as good as the 5xxx series.
- Common Applications: Roofing sheets, beverage cans, and cooking utensils.
5xxx Series (Magnesium Alloys – e.g., 5052, 5083, 5086)
- Composition: Aluminum and magnesium.
- Corrosion Resistance: Excellent, particularly in marine environments. Magnesium adds strength without greatly compromising the corrosion resistance.
- Common Applications: Marine applications, transportation industry, pressure vessels, and storage tanks for chemical products.
6xxx Series (Magnesium and Silicon Alloys – e.g., 6061, 6063)
- Composition: Aluminum, magnesium, and silicon.
- Corrosion Resistance: Good general corrosion resistance with balanced properties of strength and workability. Not as resistant to marine corrosion as the 5xxx series but widely used due to other advantageous properties.
- Common Applications: Structural applications, architectural, bridge railing, pipelines, and railway carriages.
7xxx Series (Zinc Alloys – e.g., 7075)
- Composition: Aluminum and zinc, sometimes with small amounts of magnesium and copper.
- Corrosion Resistance: Very strong but more susceptible to stress-corrosion cracking and fatigue corrosion. High strength but requires careful consideration of corrosion resistance, often treated or coated to prevent corrosion.
- Common Applications: Aerospace and defense applications where high strength-to-weight ratio is essential and corrosion prevention measures can be applied.
Effects of Surface Treatments on Aluminium
Surface treatments significantly enhance aluminium’s corrosion resistance and overall durability. Here’s a detailed look at various treatments:
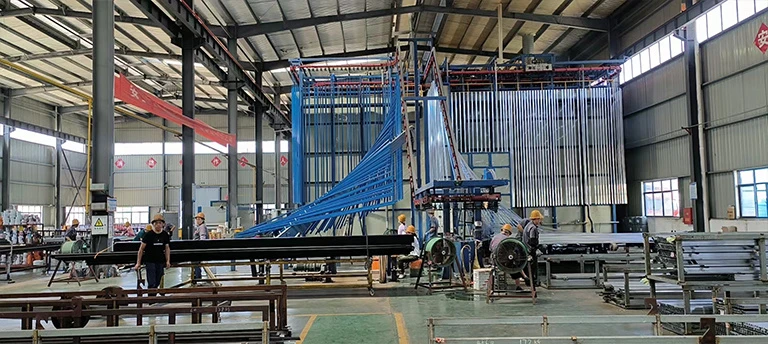
- Process: Anodizing is an electrochemical process that increases the thickness of the natural oxide layer on aluminium.
- Benefits:
- Corrosion Resistance: The thicker oxide layer provides superior protection against corrosion.
- Wear Resistance: It also improves the wear resistance of the aluminium surface.
- Aesthetic Options: Allows for coloring, offering both protective and decorative functions.
- Applications: Architectural components, automotive parts, consumer electronics.
- Process: Applying liquid paint to the aluminium surface. This can be done using various techniques, including spray, brush, or dip.
- Benefits:
- Corrosion Barrier: Creates an additional barrier to environmental factors, preventing moisture and contaminants from reaching the metal.
- Aesthetic Flexibility: Wide range of colors and finishes available.
- Applications: Construction materials, signage, consumer goods.
- Process: A dry powder is electrostatically applied and then cured under heat to form a hard coating.
- Benefits:
- Durable Finish: Offers a thicker, more durable layer compared to traditional paint.
- Environmental Protection: Excellent resistance to chipping, scratching, and corrosion.
- Applications: Automotive parts, outdoor furniture, appliances.
Protection of Marine Aluminium
In marine environments, additional steps are necessary to protect aluminium. For shipbuilding, marine-grade aluminium alloys are commonly used. These alloys, combined with surface treatments such as anodizing and protective coatings, significantly mitigate the damaging effects of seawater. Sacrificial anodes, made of zinc or magnesium, are often employed to protect aluminium hulls. These anodes corrode preferentially, sparing the aluminium—a technique known as cathodic protection. Regular maintenance and inspection are also critical to identify and address any early signs of corrosion.
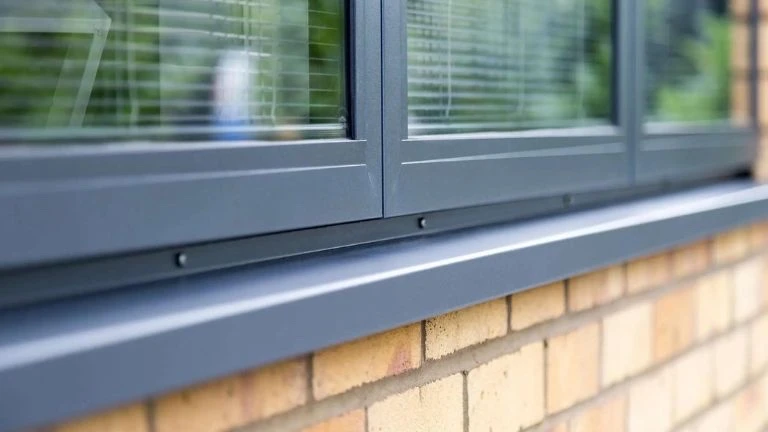
Summary
While aluminium does not rust in the traditional sense, it is susceptible to various forms of corrosion depending on the environmental conditions and the specific alloy composition. The formation of a protective oxide layer offers substantial protection in many environments, but factors like humidity, chemical exposure, and seawater pose more significant challenges. Through the use of appropriate alloys and surface treatments, aluminium’s resistance to corrosion can be markedly improved, making it a durable and reliable choice in a wide array of applications, including the marine industry. Understanding these factors allows for the effective utilization and preservation of aluminium in diverse settings.