Surface Metal Plating for Aluminum Profiles
Advantages of Metal Plating aluminum Profile
In modern industrial manufacturing, aluminum profiles are widely recognized for their lightweight, high strength, and corrosion resistance, making them invaluable in fields such as construction, transportation, electrical engineering, and electronics. These inherent properties have made aluminum profiles a preferred choice in numerous applications that demand high performance.
To further improve their functionality and aesthetic appeal, surface finish has become increasingly vital. By depositing various metal coatings, aluminum profiles can gain additional features, including enhanced decorative appearance, wear resistance, corrosion protection, and electrical conductivity. Common plating options, such as nickel, chrome, silver, tin, copper, and gold, enable tailored solutions to meet the diverse demands of industrial applications.
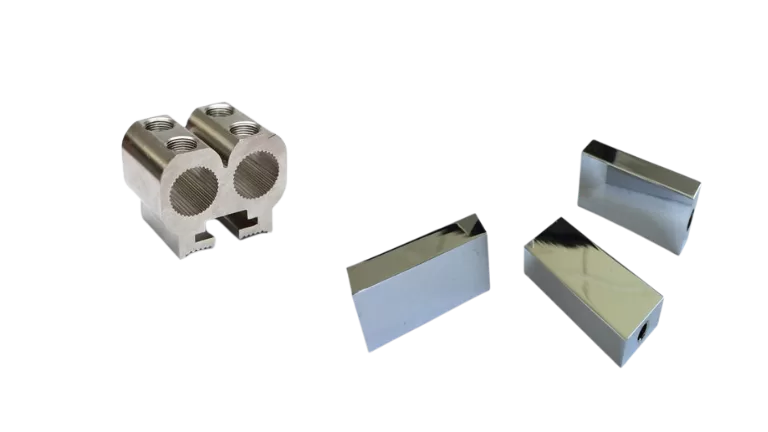
Metal Plating Process
The process of metal plating on aluminum profiles involves several steps due to their unique characteristics. Aluminum tends to naturally form a dense oxide layer upon exposure to air, which complicates the plating process. To address this, a pre-treatmentstage is necessary, involving oxide layer removal and chemical preparation of the surface. Following this, the chosen metal is deposited onto the aluminum through electrochemical methods, creating a uniform and durable metal coating. This multi-step process ensures that the aluminum profiles achieve the desired properties and meet the specific demands of their intended applications.
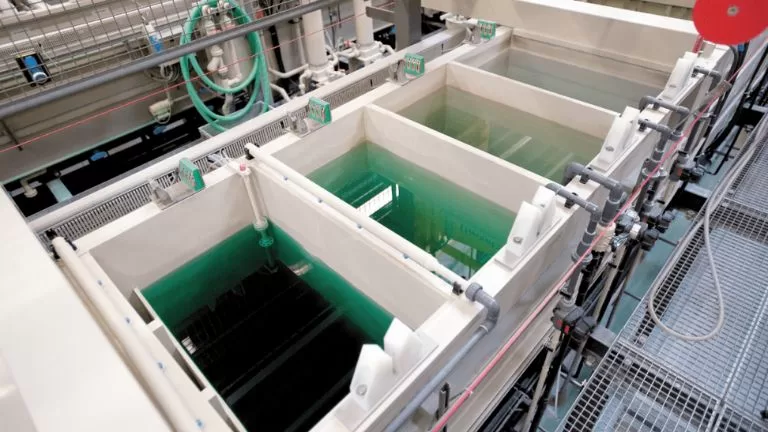
Nickel Plating Aluminum Profile
Enhancing Corrosion and Wear Resistance
Nickel plating is one of the most commonly used surface treatments for aluminum profiles, offering a balance of functionality and aesthetic versatility.
Key Advantages
- Corrosion and Wear Resistance: The dense and smooth nickel layer significantly improves the aluminum profile’s resistance to oxidation and wear.
- Enhanced Surface Hardness: Nickel plating strengthens the aluminum surface, prolonging its service life.
- Versatile Finish: Can provide either a shiny or matte appearance, suitable for both decorative and functional applications.
Applications
Nickel-plated aluminum profiles are widely used in automotive parts, household appliance casings, and electronic components that require long-term protection.
Process Considerations
Nickel plating can be performed through electroplating or electroless plating (chemical plating). Proper surface preparation is essential to ensure strong adhesion between the nickel layer and the aluminum substrate.
Chrome Plating Aluminum Profiles
Superior Decorative and Wear Resistance
Chrome plating is a highly decorative and durable surface treatment, known for its bright mirror-like finish and outstanding wear resistance.
Key Advantages
- Aesthetic Appeal: Chrome creates a high-gloss, reflective surface, ideal for decorative applications.
- Durability: Thin yet hard, the chrome layer provides excellent resistance to scratches and corrosion.
- Long-Lasting Protection: Suitable for components exposed to harsh environments.
Applications
Commonly used in automotive trim, motorcycle parts, high-end appliances, and architectural elements requiring both performance and visual appeal.
Process Considerations
Due to aluminum’s high reactivity, a base layer of copper or nickel is typically applied before chrome plating to ensure a smooth, durable, and uniform chrome layer.
Silver Plating Aluminum Profiles
Enhancing Conductivity and Solderability
Silver plating is ideal for applications requiring exceptional electrical and thermal conductivity. It is widely used in industries such as electronics, renewable energy, and medical devices.
Key Advantages
- High Conductivity: Silver offers the highest electrical and thermal conductivity among all metals, making it ideal for power and electronic components.
- Solderability: Silver plating ensures excellent welding and soldering performance.
- Antimicrobial and Decorative Properties: Silver also provides a hygienic surface and a polished, luxurious appearance.
Applications
Used in electrical connectors, busbars, medical equipment, and high-end decorative components.
Process Considerations
To ensure strong adhesion, a pre-treatment layer (such as nickel) is often applied before silver plating. Post-plating treatments may include anti-tarnish coatings to maintain the silver’s brightness and durability.
Tin Plating Aluminum Profiles
Optimizing Solderability and Corrosion Resistance
Tin coating is a cost-effective solution for aluminum profiles, particularly in applications requiring solderability and environmental safety.
Key Advantages
- Improved Solderability: Tin plating simplifies welding and enhances electrical connections.
- Corrosion Resistance: Protects aluminum profiles from oxidation and environmental damage.
- Non-Toxic and Safe: Tin is suitable for food-grade and environmentally conscious applications.
Applications
Commonly used in electrical terminals, wire connectors, battery connections, and food processing equipment.
Process Considerations
Tin plating is often preceded by a base layer (e.g., copper or nickel) to ensure strong adhesion and uniform coverage. The plated surface may also undergo finishing treatments to enhance its performance.
Copper Plating Aluminum Profiles
A Foundation for Conductivity and Adhesion
Copper plating is frequently used as a base layer for other plating processes or as a standalone treatment for applications requiring high conductivity.
Key Advantages
- Electrical and Thermal Conductivity: Copper is highly conductive, making it ideal for power and thermal management systems.
- Adhesion Base: Serves as a foundation for subsequent plating layers, such as nickel or silver.
- Improved Durability: Enhances wear resistance and provides moderate corrosion protection.
Applications
Used in electronic components, precision connectors, busbars, and as a preparatory layer for multi-layer plating systems.
Process Considerations
Aluminum profiles require thorough cleaning and a strike layer (e.g., zincate or nickel) to facilitate strong adhesion between the aluminum and copper layers.
Gold Plating Aluminum Profiles
Premium Protection and Exceptional Conductivity
Gold plating is a high-end surface treatment primarily used in critical applicationsrequiring long-term stability, low electrical resistance, and anti-corrosion properties.
Key Advantages
- Outstanding Corrosion Resistance: Gold is highly resistant to oxidation, ensuring long-term reliability.
- Exceptional Conductivity: Provides stable, low-resistance electrical connections.
- Luxurious Appearance: Adds a premium, elegant finish to aluminum profiles.
Applications
Commonly used in high-end electrical contacts, microelectronic components, medical instruments, and aerospace systems.
Process Considerations
Due to gold’s cost, it is typically applied as a thin layer over a base coating (e.g., nickel or copper) to achieve the desired performance while minimizing material usage.
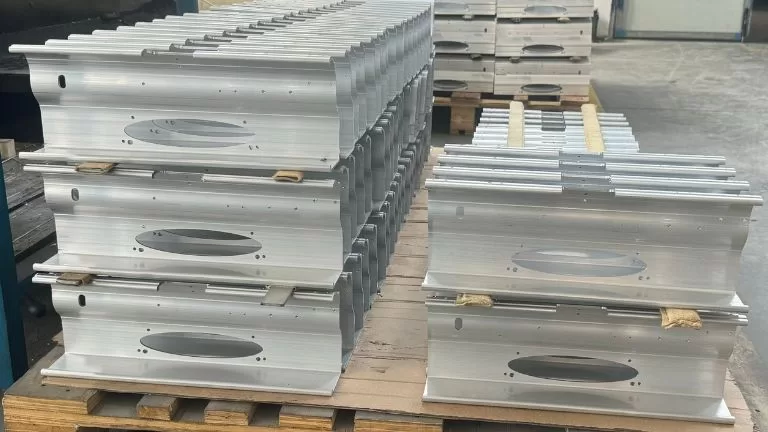
Custom Metal Plating Aluminum Profiles
At HTS-ALU, we offer comprehensive, one-stop aluminum profile customization services, covering everything from mold design and manufacturing to extrusion, CNC machining, and surface treatments, including metal plating. With our expertise and advanced capabilities, we ensure that each aluminum profile meets your exact specifications for both functionality and aesthetics.
Aluminum extrusion is a highly efficient forming process that delivers low production costs, excellent surface finish, and outstanding versatility. Extruded aluminum profiles can undergo additional precision machining to create custom aluminum components tailored to your needs. By combining extrusion with advanced surface treatments, including metal plating techniques such as nickel, chrome, and silver, HTS-ALU provides high-performance aluminum products that meet industrial, decorative, and engineering demands.
Our Factory
Our factory is equipped with 40 extrusion production lines to efficiently manufacture aluminum profile. We have one anodizing and electrophoresis line, along with two vertical spraying machines and two horizontal spraying machines for surface treatment. Additionally, we operate two sandblasting machines and six wood grain transfer printing lines, enabling us to provide various aesthetic finishes. To support our production, we also have furnaces for casting aluminum bars, aging furnaces, annealing furnaces, water cooling treatment equipment, and machining equipment, ensuring comprehensive capabilities for high-quality output.
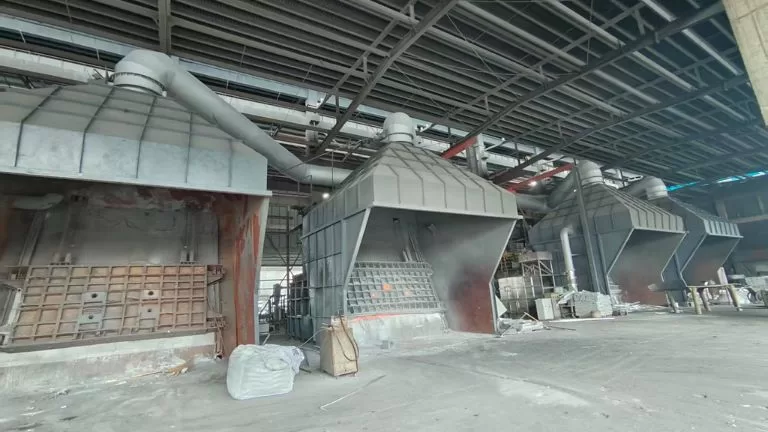
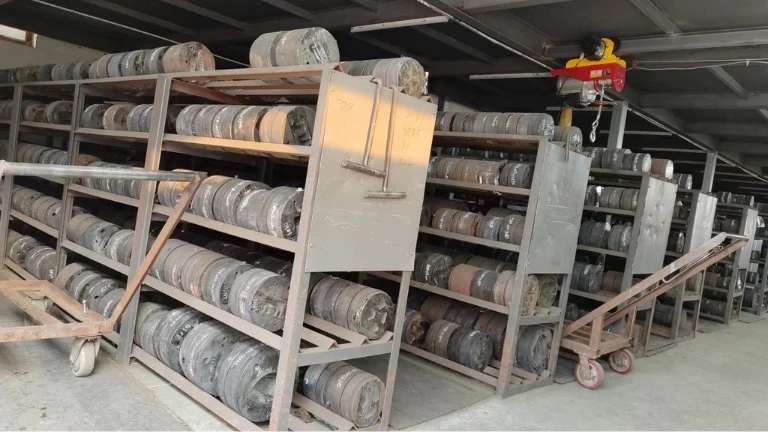
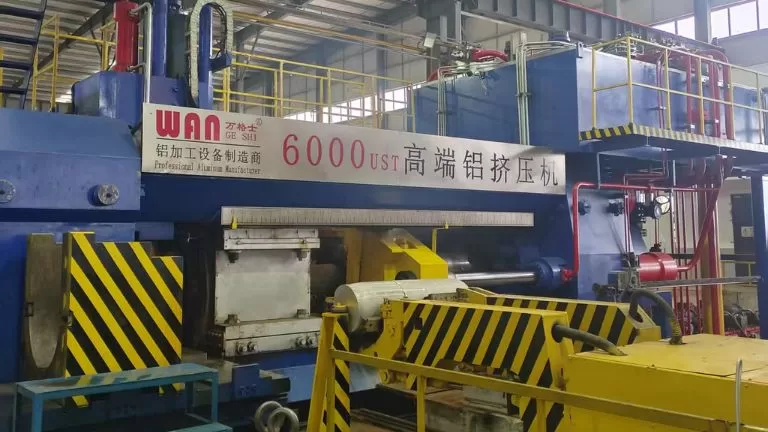
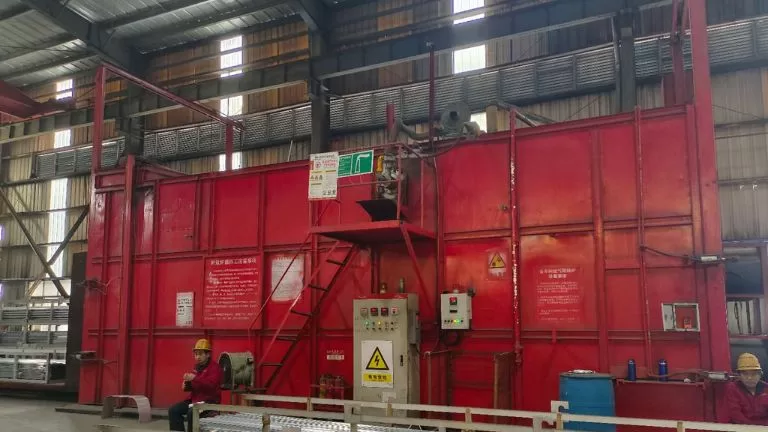
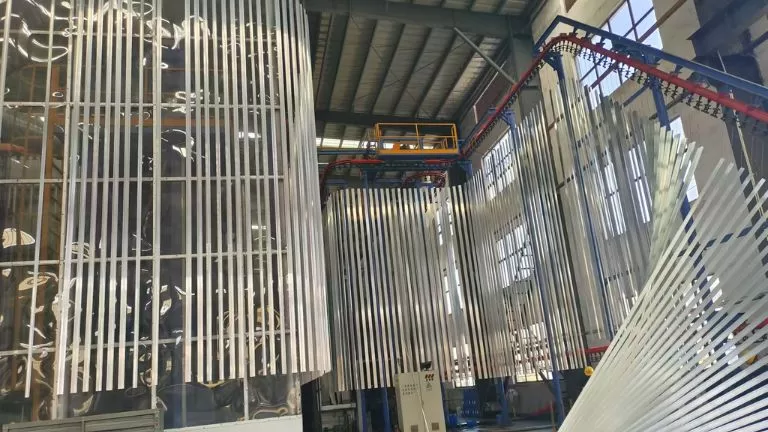
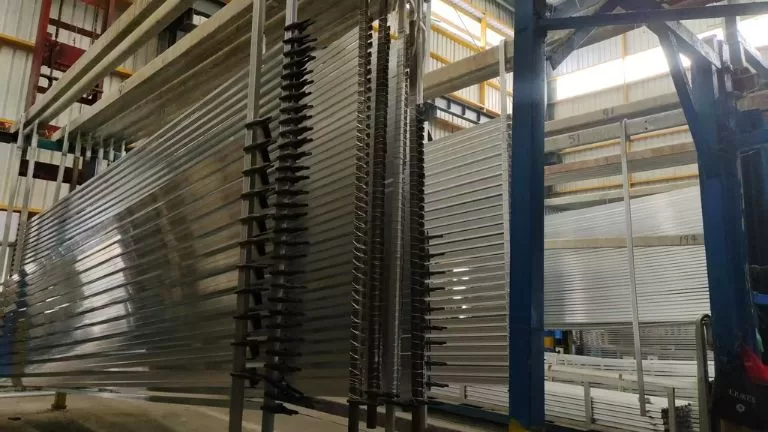
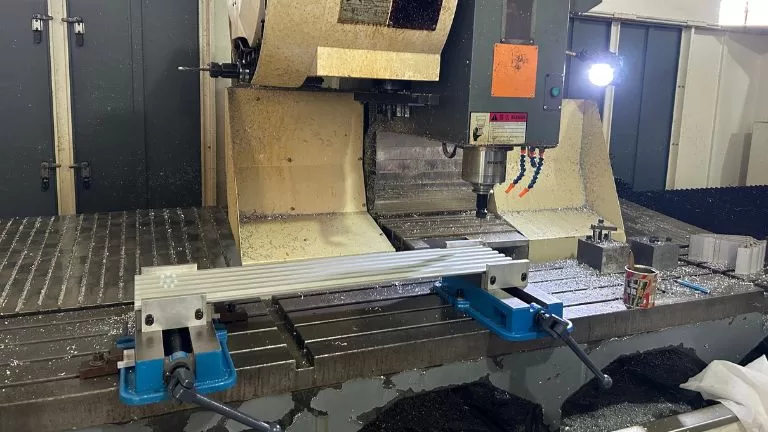
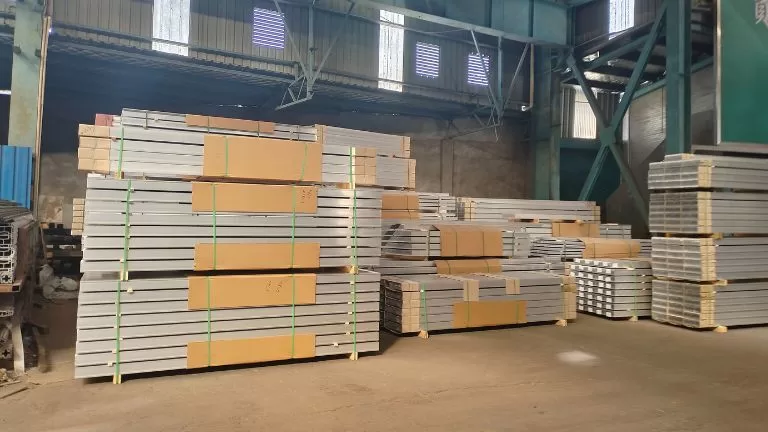