Custom Premium Telescoping Aluminum Square Tubing
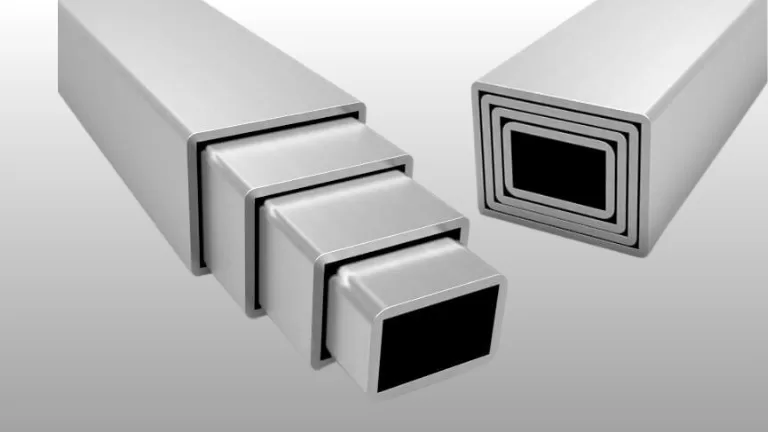
Telescoping aluminum square tubings are rectangular or square pipes made from high-precision aluminum alloy through an extrusion process. They feature uniform wall thickness, neat corners and edges, and precise dimensions. These tubes allow multiple sections of different-sized square pipes to nest together, enabling the length to be freely adjusted. They’re commonly used in structural components that require telescoping functionality.
Based in China, HTS-ALU specializes as a custom aluminum profile extrusion manufacturer, delivering diverse telescoping aluminum tubes alongside comprehensive surface treatment and precision machining solutions.
Telescoping Aluminum Square Tubing Manufacture
We are a manufacturer specializing in custom telescoping aluminum square tubes. With advanced production lines and precision machines, we provide high-quality, customized telescoping tubes in various sizes to meet your needs. Whether for industrial machinery, outdoor equipment, display racks, or stands, we offer complete services from material selection and design to surface finishing and assembly. We can work from your drawings or samples, and offer fast sampling and bulk delivery to help your products stand out in the market.
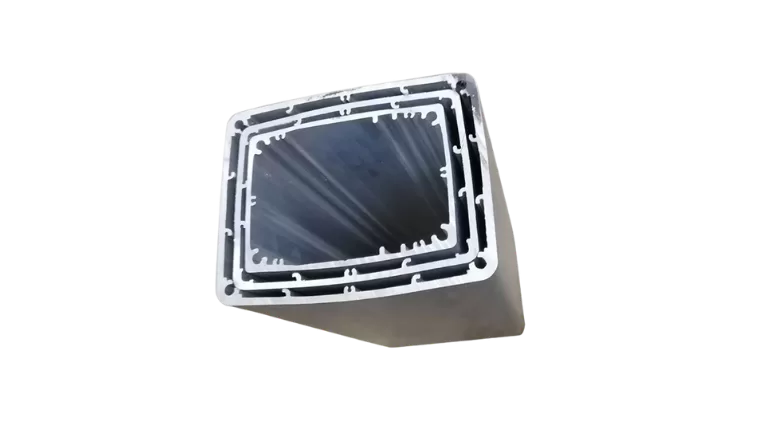
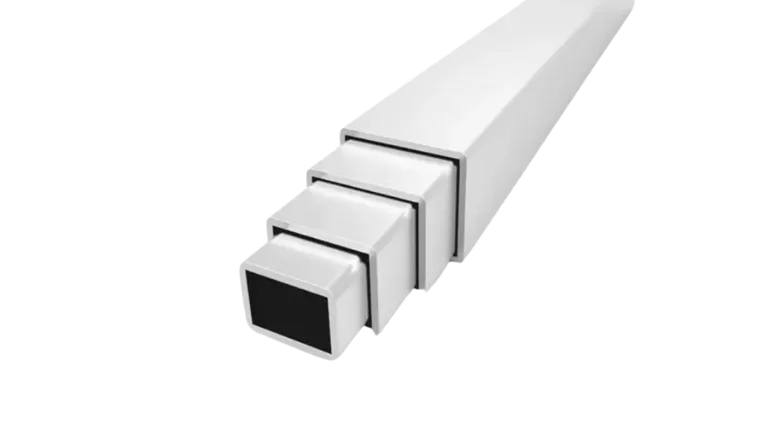
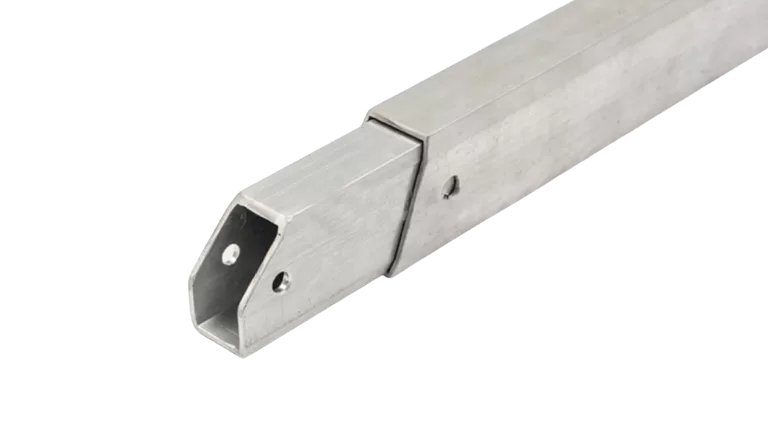
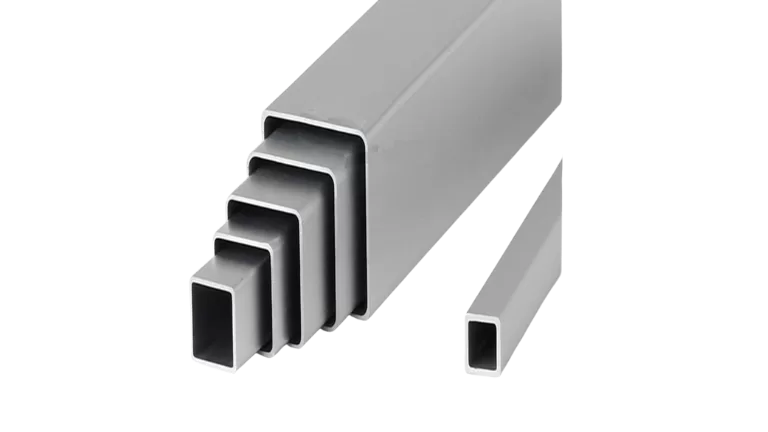
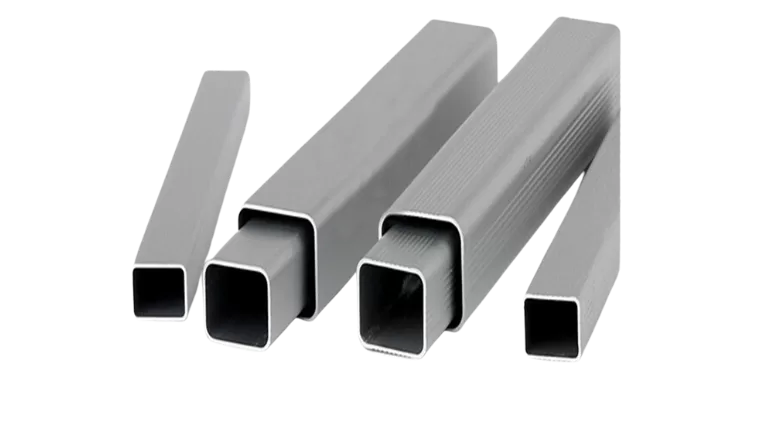
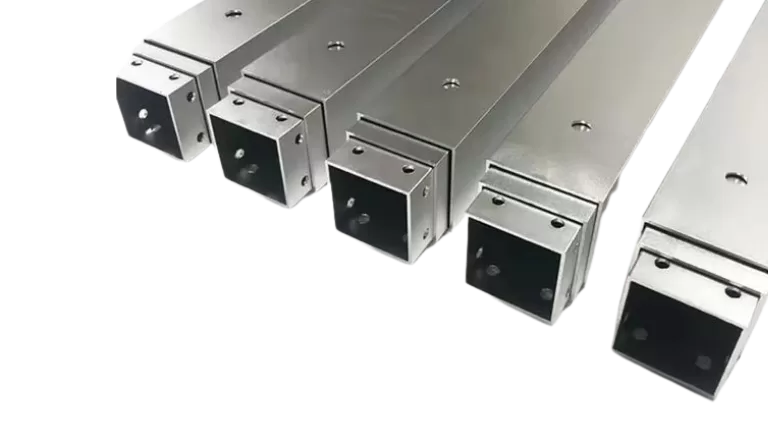
Telescoping Square Tubing Specifications
Parameter | Specification Range | Notes |
---|---|---|
Outer Size | 10 × 10 ~ 100 × 100 mm | Customizable on request |
Wall Thickness | 0.8 ~ 5.0 mm | Select as needed for strength |
Standard Length | 6.0 m | Any length can be cut |
Telescoping Stages | 2 to 5+ stages | Multi-stage nesting available |
Material | 6061/6063/custom aluminum alloy | Anodized, powder coated optional |
Tolerance | ±0.05 ~ ±0.1 mm | High precision CNC machining |
Applications of Telescoping Aluminum Square Tubing
Telescoping aluminum square tubes are widely used across different fields because of their light weight, high strength, corrosion resistance, and adjustable length. We provide telescoping tubes in different designs to meet a variety of needs:
- Industrial automation: telescoping drive rods, guide brackets, etc.
- Outdoor equipment: tent frames, camera tripods, and more
- Transportation and logistics: adjustable racks, telescoping trailer supports, and so on
All our telescoping aluminum tubes can be customized. From material selection and structure to surface finish, we offer tailored solutions for the unique requirements of every industry, helping your products stand out in the market.
Materials for Telescoping Aluminum Square Tubes
1. 6061 aluminum alloy: Used in our telescoping square tubings, contains magnesium (0.8–1.2%) and silicon (0.4–0.8%), forming magnesium silicide for excellent strength-to-weight ratio and corrosion resistance. Magnesium boosts strength without adding weight; silicon improves machinability and enables precise extrusion. Chromium (0.04–0.35%) further increases corrosion resistance, while copper (0.15–0.4%) adds extra strength while maintaining durability. These properties make 6061 alloy ideal for customizable, lightweight, and durable telescoping aluminum tubes used in various demanding environments.
2. 6061 aluminum alloy: Often referred to as an architectural alloy, this aluminum alloy features a smooth surface finish and is widely used in window and door frames. With key elements including silicon (0.20–0.60%), magnesium (0.45–0.90%), and minimal amounts of copper, chromium, zinc, titanium, and manganese, it offers a good combination of formability, corrosion resistance, and strength. When applied to telescoping aluminum square tubes, this alloy not only ensures a sleek appearance but also provides the durability and dimensional stability needed for adjustable structures, making it ideal for both architectural and versatile engineering applications.
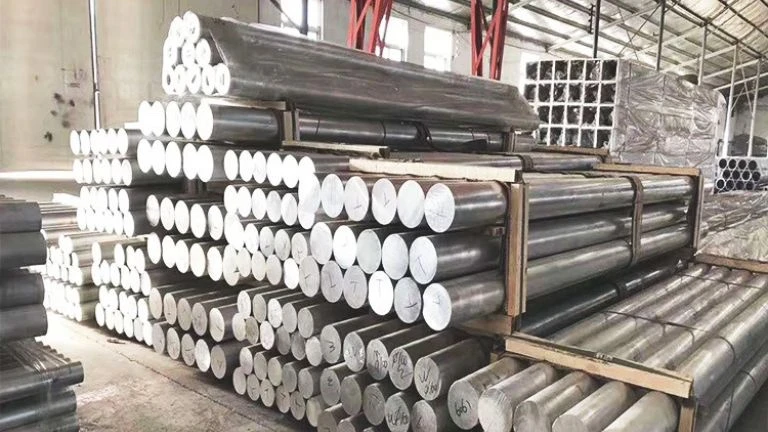
Surface Treatment Process
For telescoping aluminum square tubes, various surface treatment processes are used to enhance performance and aesthetics.
1. Anodizing improves corrosion resistance and surface hardness while offering a range of colors such as silver, black, gold, and gray.
2. Powder coating provides a thicker, scratch-resistant, and UV-resistant finish with diverse color options.
3. Sandblasting or brushed finishes elevate the texture and effectively prevent fingerprints, giving the tubes a more refined look.
4. Conductive or functional coatings can be applied to meet the specific requirements of electronic or mechanical applications.
These treatments ensure that telescoping aluminum tubes are not only durable and visually appealing but also adaptable to specialized industrial and architectural needs.

Precision Machining Processes
With the following sophisticated manufacturing processes, our telescoping aluminum square tubes combine high precision, strong adaptability, and reliable quality, making them widely applicable across various industries.
1. High-precision extrusion:
Advanced molds and processes ensure that each tube section has consistent and accurate dimensions.
2. CNC machining:
We can customize your tubes with chamfering, slotting, drilling, tapping, cutting, milling grooves, and more—according to your requirements.
3. End processing:
Tube ends can be finished with internal threads, external threads, or connector sleeves to meet different assembly or connection needs.
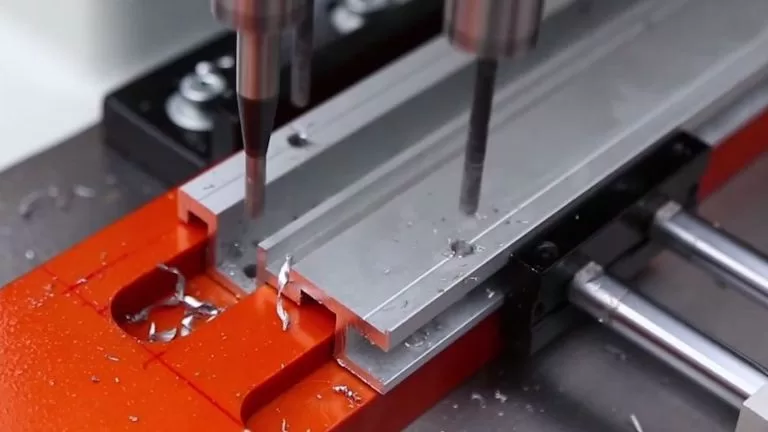
Features of Telescoping Aluminum Square Tubing
A versatile core component for industrial and civilian use, combining functionality and reliability with these key advantages:
1. Adjustable Length: Multi-section nested design allows free length adjustment.
2. Lightweight & Strong: Aluminum alloy offers low weight with high load capacity.
3. Corrosion-Resistant: Anti-rust and oxidation-resistant for long-term durability.
4. High Precision: CNC and precision molds ensure tight tolerances (±0.03mm).
5. Aesthetic Options: Surfaces can be finished in glossy, matte, or colored styles.
leading manufacturer from China
Custom Extruded Aluminum Telescoping Square Tubings
Our aluminum extrusion factory is located in Nanchang, Jiangxi Province, covering 30,000 square meters and staffed by more than 120 skilled workers. We specialize in producing telescopic aluminum square tubings and are committed to high product quality. We follow strict environmental standards to protect the environment and provide a safe, supportive workplace for our employees. By choosing us, you get reliable telescopic aluminum tubings from a manufacturer who truly values both sustainability and employee well-being.
Advanced Extrusion Lines
Boasting over 30 high-precision extrusion production lines from Japan and Germany, we ensure unmatched quality and efficiency.
Custom Mold Design and Processing
We create custom molds according to your designs or samples and offer prototypes for approval, ensuring all specifications are met accurately.
Comprehensive Surface Treatment Techniques
We provide a variety of surface treatments, including anodizing, electroplating, and powder coating, to enhance both durability and aesthetic quality.
Over Two Decades of Expertise
Established in 2013, we specialize in aluminum profiles for windows, doors and industrial applications, with years of proven expertise.
Factory Show
Our factory features 40 extrusion lines for efficient aluminum profile production. We offer a full range of surface treatments—including anodizing, electrophoresis, powder coating, sandblasting, and wood grain transfer printing—with advanced equipment. In-house casting, aging, annealing, water cooling, and machining ensure complete control and high-quality results for all products.
RFQ of Extruded Tlescoping Aluminum Pipe
1. Accurately assess the load-bearing requirements: Based on the actual load conditions, precisely select the suitable aluminum alloy material (such as 6061, 6063, etc.), and rationally plan the wall thickness of the tube to ensure it meets the requirements of strength and rigidity.
2. Determine the number of nested sections and dimensional tolerances: According to the telescopic stroke requirements, determine the number of sections in the multi-stage nested structure. And based on the assembly precision requirements, select the matching tube dimensions and strict tolerance control (such as ±0.03mm) to ensure smooth telescoping and precise positioning.
3. Choose the surface treatment according to the environment: Considering the usage environment (such as outdoors, industrial settings, indoor decoration, etc.), select the appropriate surface treatment process (anodizing, powder coating, sandblasting, etc.) to enhance the corrosion resistance, aesthetics, and functionality of the tubes.
4. Customize for special connections and functions: For special connection requirements (such as quick connectors, snap fasteners, positioning pins, etc.) or functional requirements (conductive, antistatic, etc.), communicate with the design team in advance to customize and process exclusive components, ensuring that the product perfectly adapts to the application scenario.
1. Daily Cleaning: Wipe with a damp cloth; avoid using steel wool (to protect the anodized layer).
2. After Exposure to Extreme Environments: Rinse with a neutral cleaner after exposure to coastal or dusty environments, then dry and apply a thin layer of lubricant (silicone oil preferred).
3. Long-Term Storage: Collapse to the shortest state to avoid prolonged pressure from gravity, which can lead to metal fatigue.
. Anodizing (Oxidation)
- Common Colors:
Natural silver
Black
Champagne
Light bronze
Dark bronze
Gold
2. Electrophoresis Coating (E-Coating)
- Common Colors:
Black
Champagne
Light bronze
Dark bronze
Custom metallic colors
3. Powder Coating
- Colors:
Can match any color based on the RAL color chart.
Offers textures like matte, gloss, satin, and custom finishes.
4. PVDF Coating (Polyvinylidene Fluoride)
- Colors:
Also customizable using the RAL color chart.
High-end finishes with matte or glossy effects.
5. Wood Grain Transfer Printing
- Colors and Patterns:
Mimics various wood types (e.g., oak, walnut, teak, mahogany).
Custom patterns available based on provided samples.
6. Film Lamination
- Colors and Patterns:
Includes textures like marble, leather, and solid colors.
Custom finishes and patterns based on provided samples.
Pre-Treatment Options (Impact on Final Color)
- Brushing/Polishing: Produces smooth or reflective metallic surfaces.
- Sandblasting: Adds a rough, matte texture before the final surface treatment.
Mold fees are an essential part of the custom aluminum extrusion process. Since every order requires a uniquely designed mold tailored to specific requirements, these molds cannot be used for other products. Therefore, the mold fee is necessary and non-negotiable.
We require 100% upfront payment of the mold fee before mold development begins to ensure timely production. However, as a token of appreciation for your support, we offer a refund of the mold fee or equivalent discounts once the order reaches a certain production volume. Specific policies can be discussed based on your order volume and collaboration details.
Mold production typically takes 7 days. After the sample is confirmed, producing a full container load of 26 tons generally requires 14 days for extrusion alone. If surface treatment is required, an additional 3 days will be needed. For machining, extra time will be required depending on the complexity and volume of the machining work. The exact additional time for machining will be determined based on the specific processing requirements.
Aluminum profiles are naturally corrosion-resistant due to the formation of a thin, protective oxide layer when exposed to air or water. This oxide layer is stable and self-repairing, meaning that even if the surface is scratched or cut (such as at exposed ends or during processing), the aluminum will not rust or corrode like iron or steel. Instead, the exposed areas will quickly form a new oxide layer, providing continuous protection against further oxidation.
With proper design, installation, and maintenance, aluminum profiles can last for decades, even in challenging environments. For example, untreated aluminum can easily withstand 20-30 years in outdoor applications, while profiles with surface treatments like anodizing or powder coating can last even longer, often exceeding 50 years. This makes aluminum an excellent choice for applications where durability and long-term performance are essential.
The price of aluminum profiles consists of several components: raw material costs, extrusion processing fees, surface treatment fees, machining costs, and additional packaging fees. Among these, the cost of aluminum as a raw material tends to fluctuate frequently, while other fees remain relatively stable. Due to these fluctuations, our quotations are typically valid for 7 days.
Pricing can be structured in different ways depending on the product and requirements. It can be calculated by weight (e.g., cost per ton), by length (e.g., cost per meter), or by piece (e.g., cost per unit). For products involving extensive machining, such as heat sinks, pricing is generally calculated on a per-piece basis to accurately reflect the additional processing costs. This flexible pricing approach ensures the quote is tailored to the specific needs of the customer.
We can manufacture aluminum profiles in compliance with technical requirements that meet European standards (EN), American standards (ASTM/AA), or other standards as specified by the customer. Custom production is tailored to ensure that the profiles meet the specific standard requirements requested.
Our production equipment is designed for the metric system. If the drawings provided are in the imperial system, we will convert them into metric units for production to ensure accuracy.
It is important to note that while we can machine imperial-threaded holes for fasteners, if you require us to supply matching imperial fasteners, they may not always be available in stock. Custom orders for imperial fasteners typically require a large volume for production. Please consider this when planning your project.